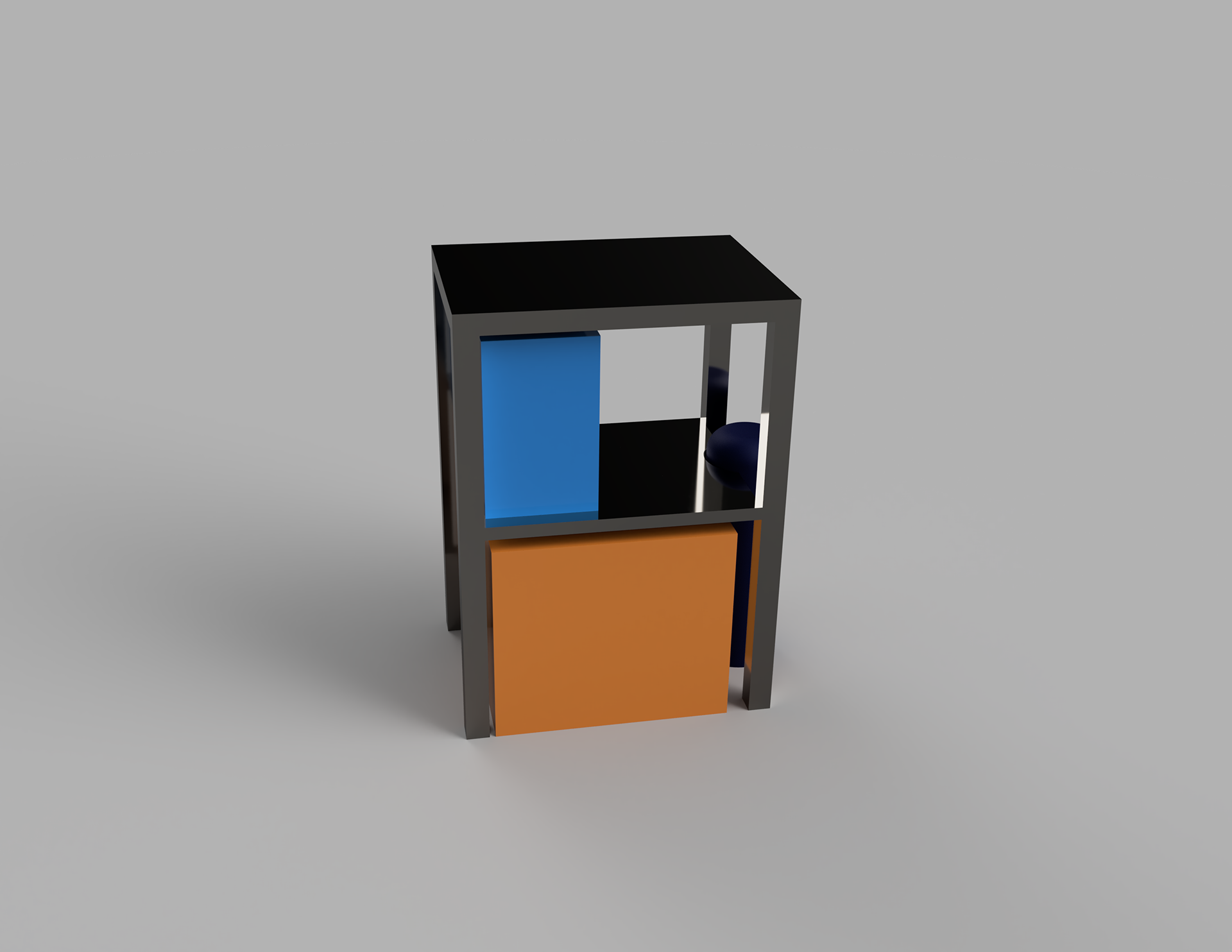
The Concept: I wanted to build a metal fabrication and welding table that could save space in my small one car garage workshop.
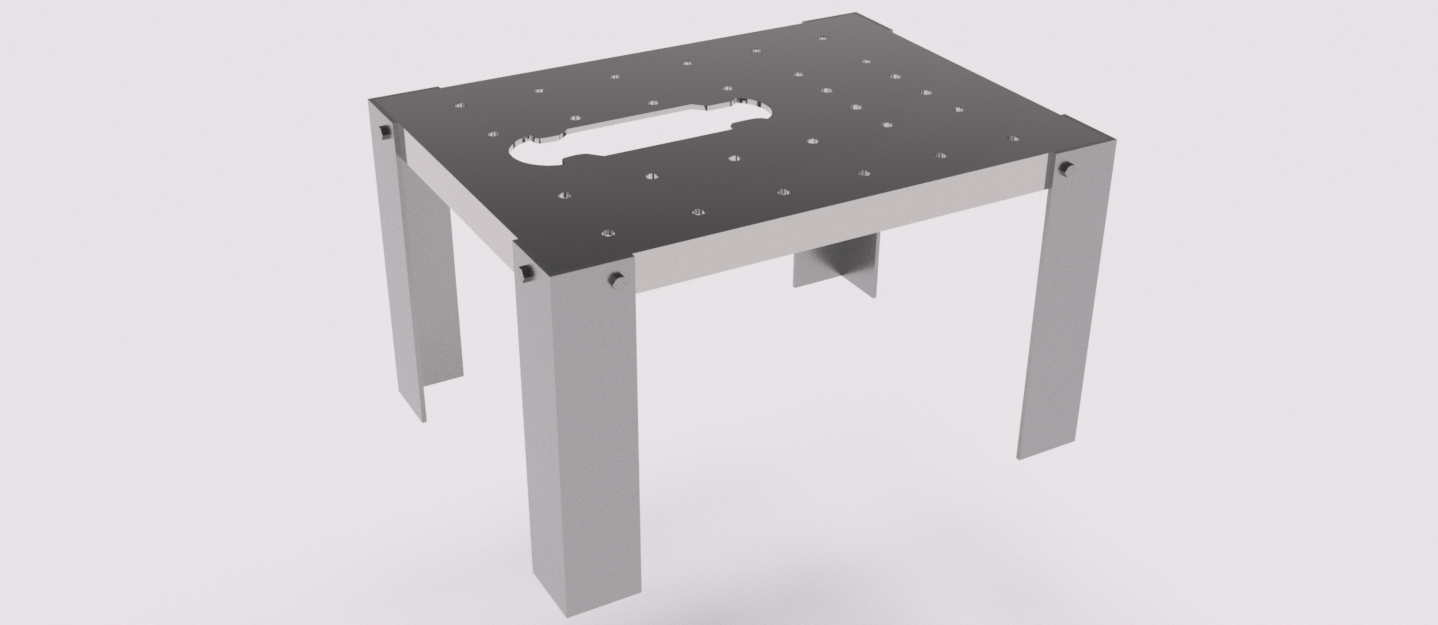
I also wanted fixture holes for clamping workpieces and tools to the table top. I also decided to split the legs into angle iron uppers and square tube lowers so the height could be adjustable. I also wanted the table to be easy to disassemble for when I move. This render reflects these changes (lowers not shown).
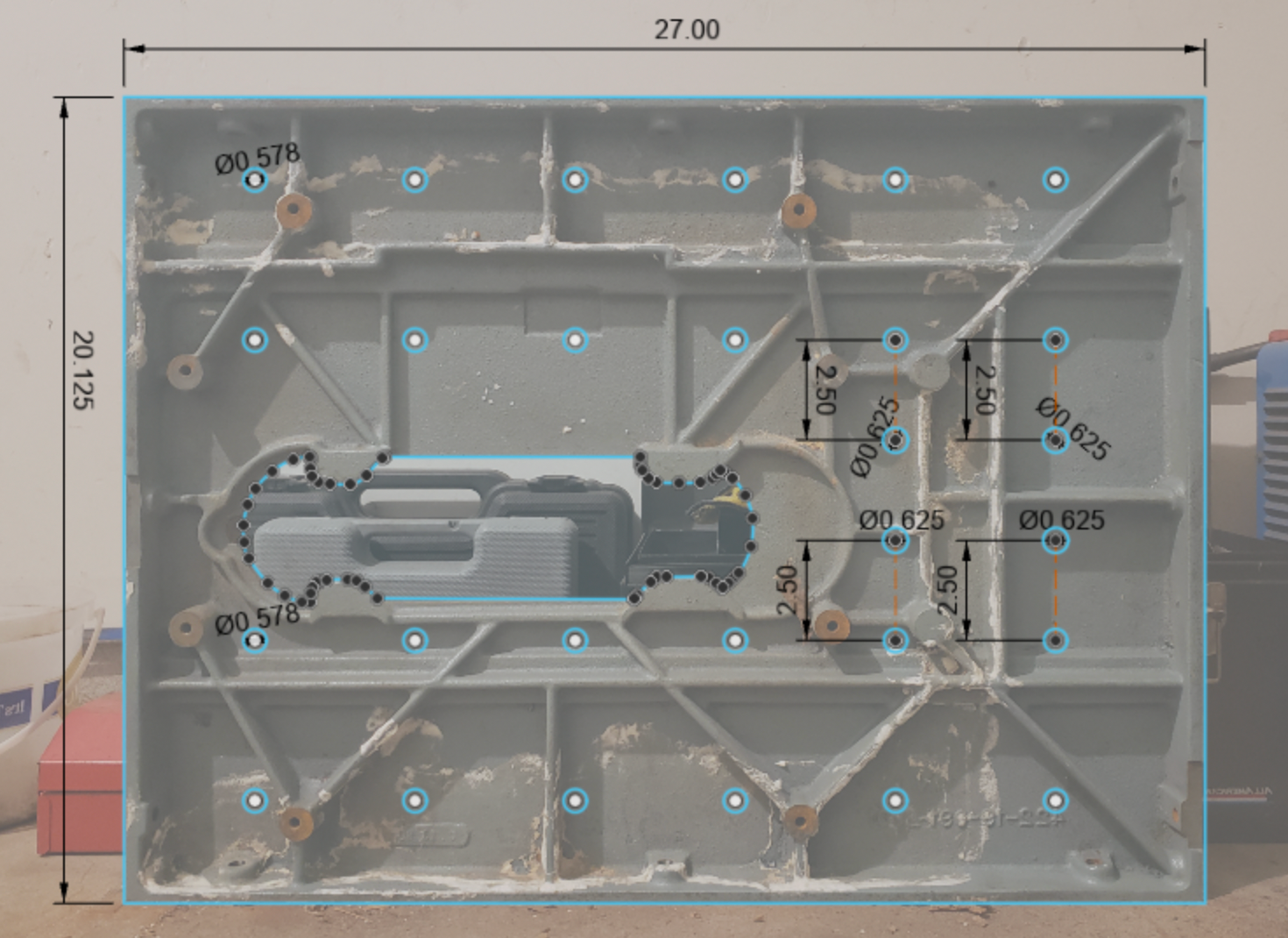
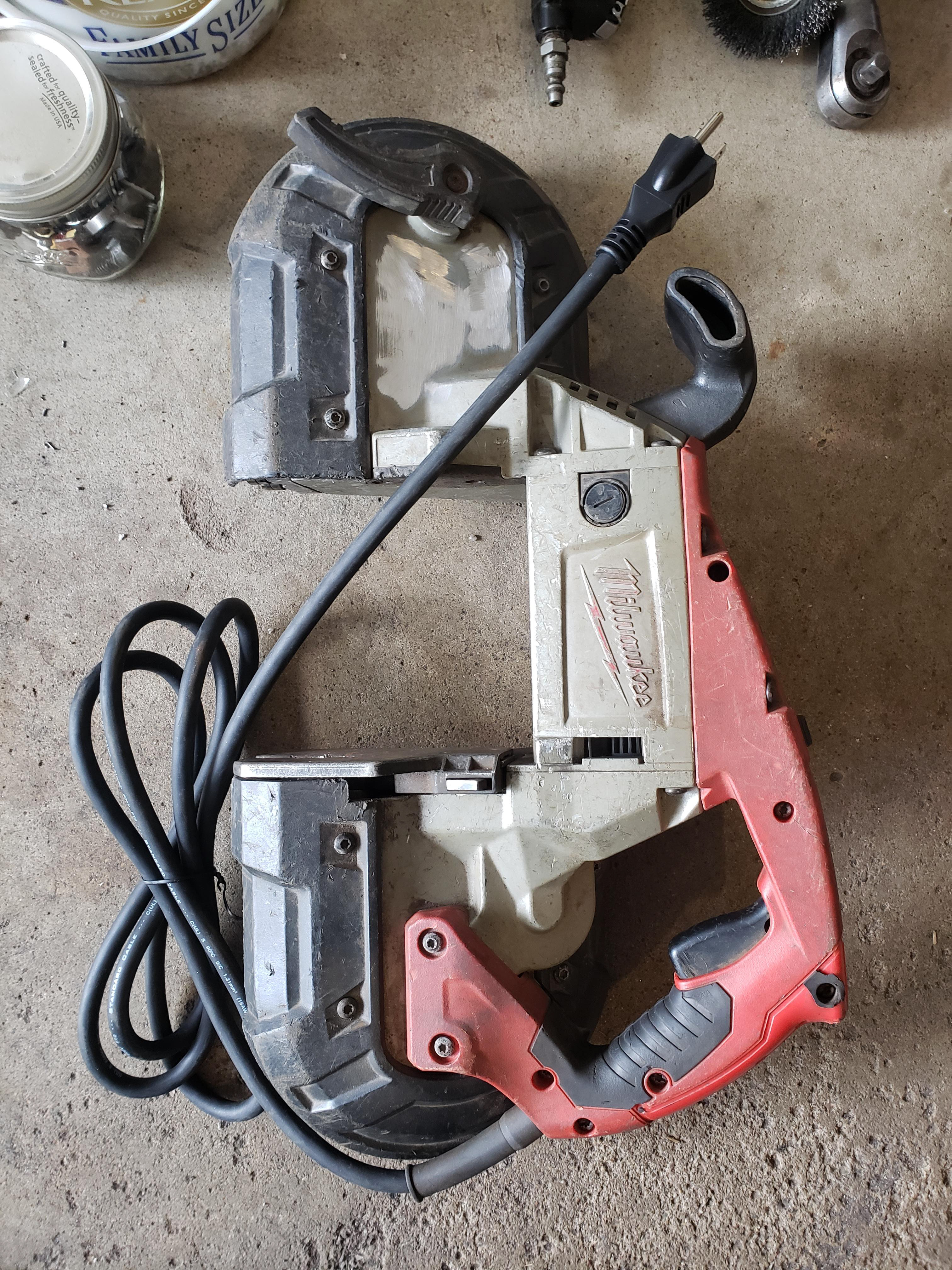
I purchased a used Milwaukee portable band saw. They're one of the most affordable saws capable of cutting steel, offer great versatility in the shapes they can cut unlike an abrasive chop saw, and blades are cheap and plentiful. I plan to build a table for it to convert it to a vertical band saw once this workbench is complete. In the meantime, it was very useful in cutting the thick stock for the table legs amongst other tasks.
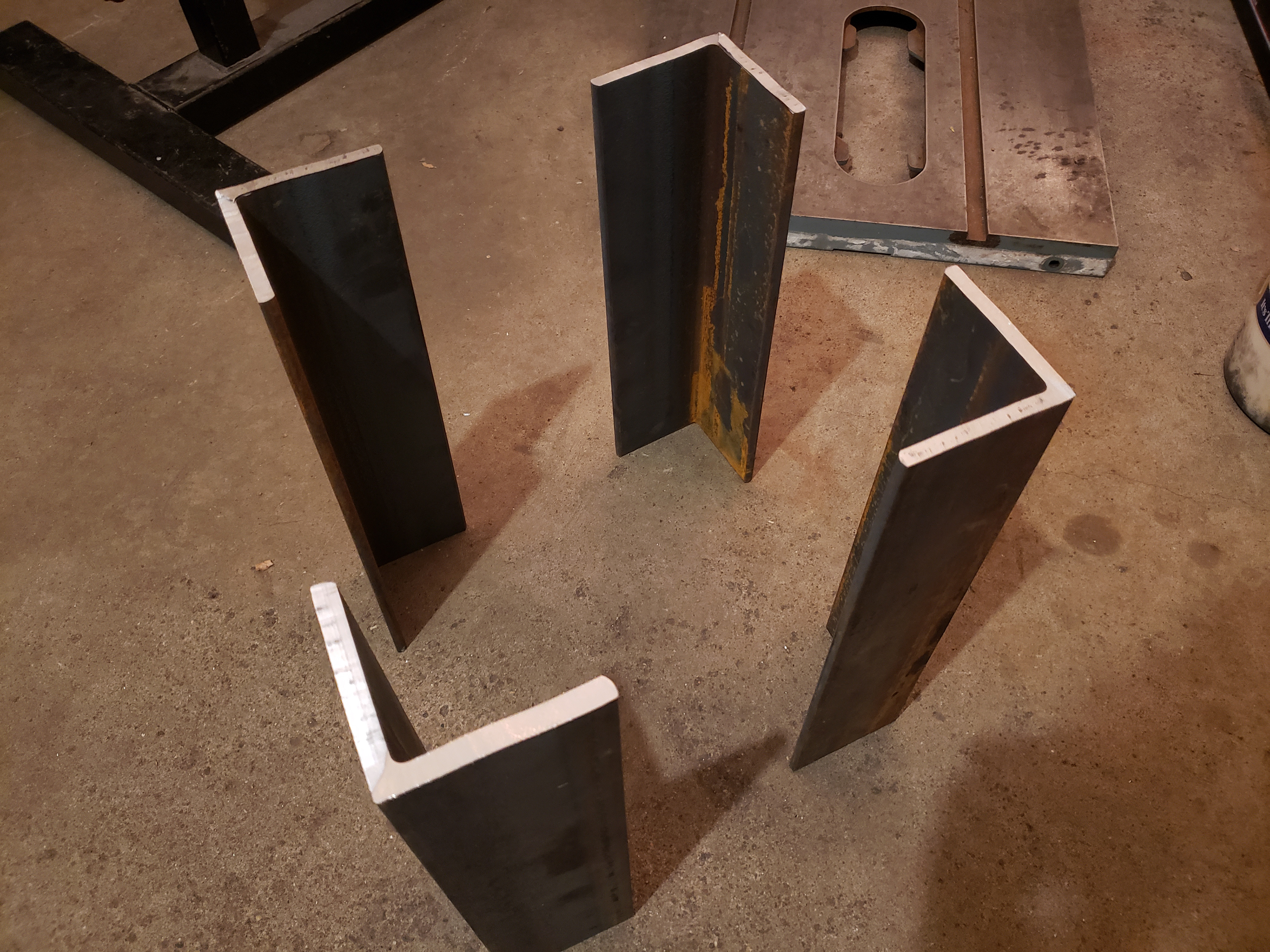
Upper legs all cut! Note all the mill scale and rust. This dull grayish oxide coating is a product of the hot rolling manufacturing process. The mill scale is much harder than the steel beneath it and quickly clogs flap discs which are how I initially approached removing the scale.
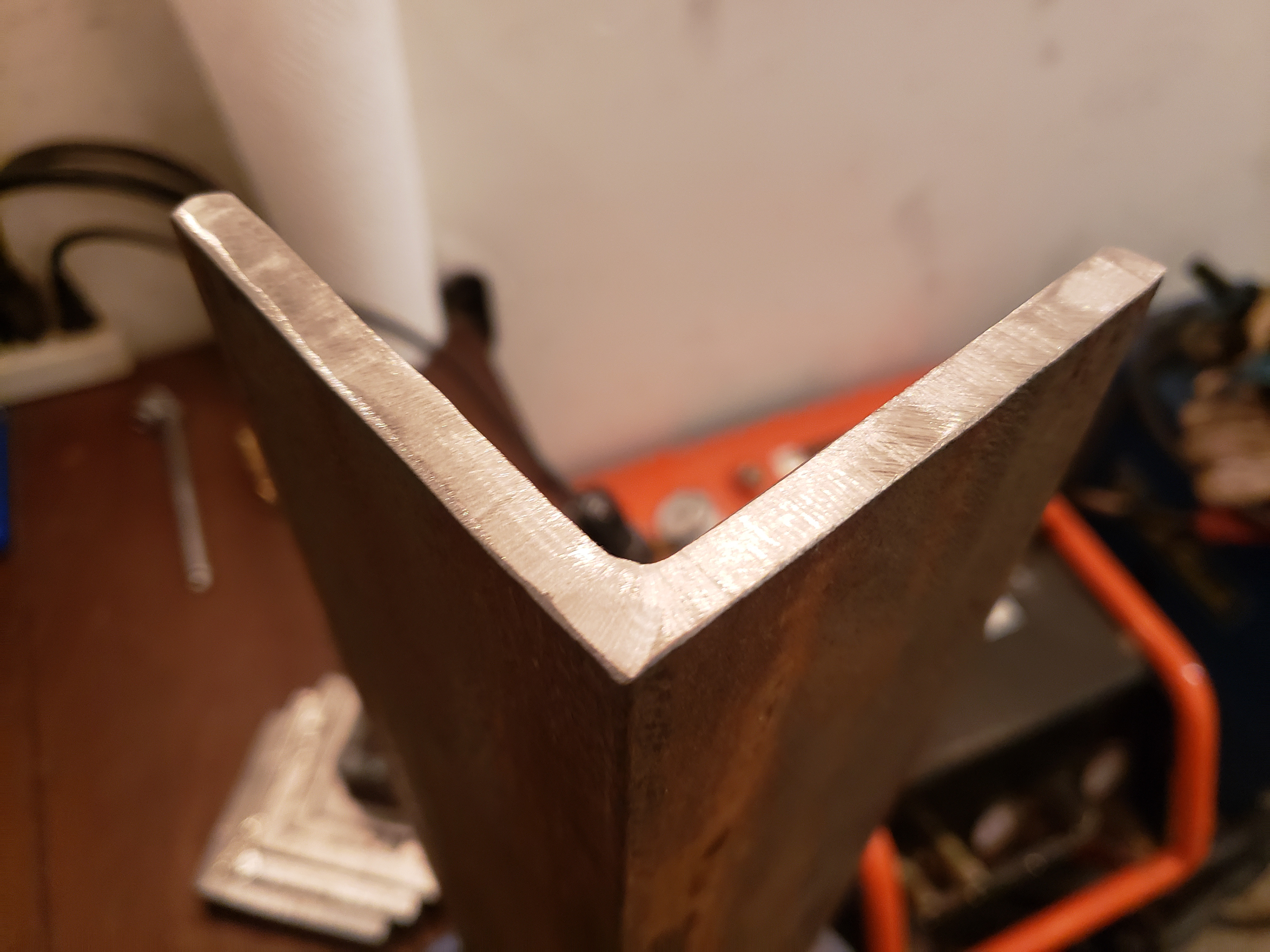
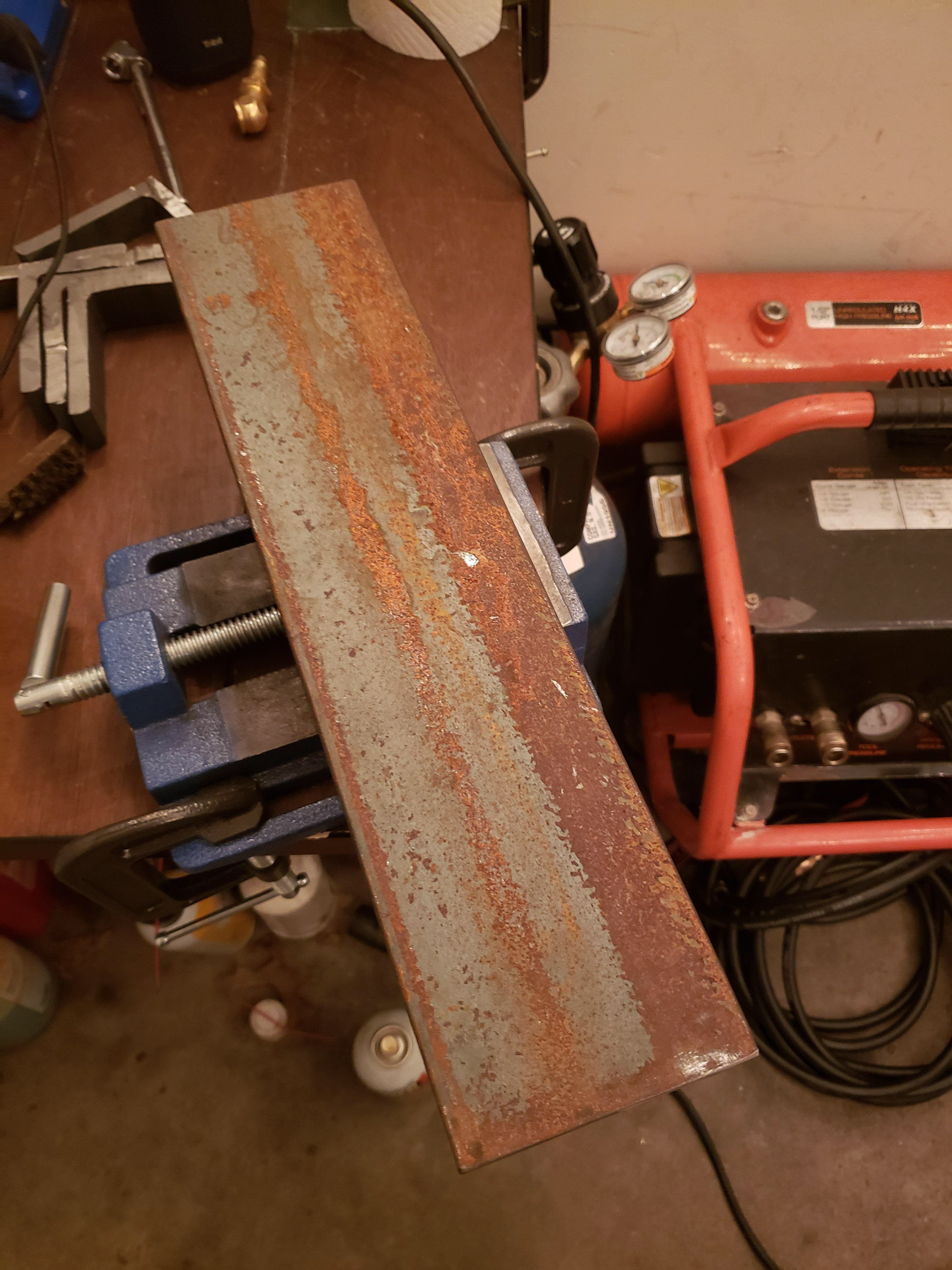
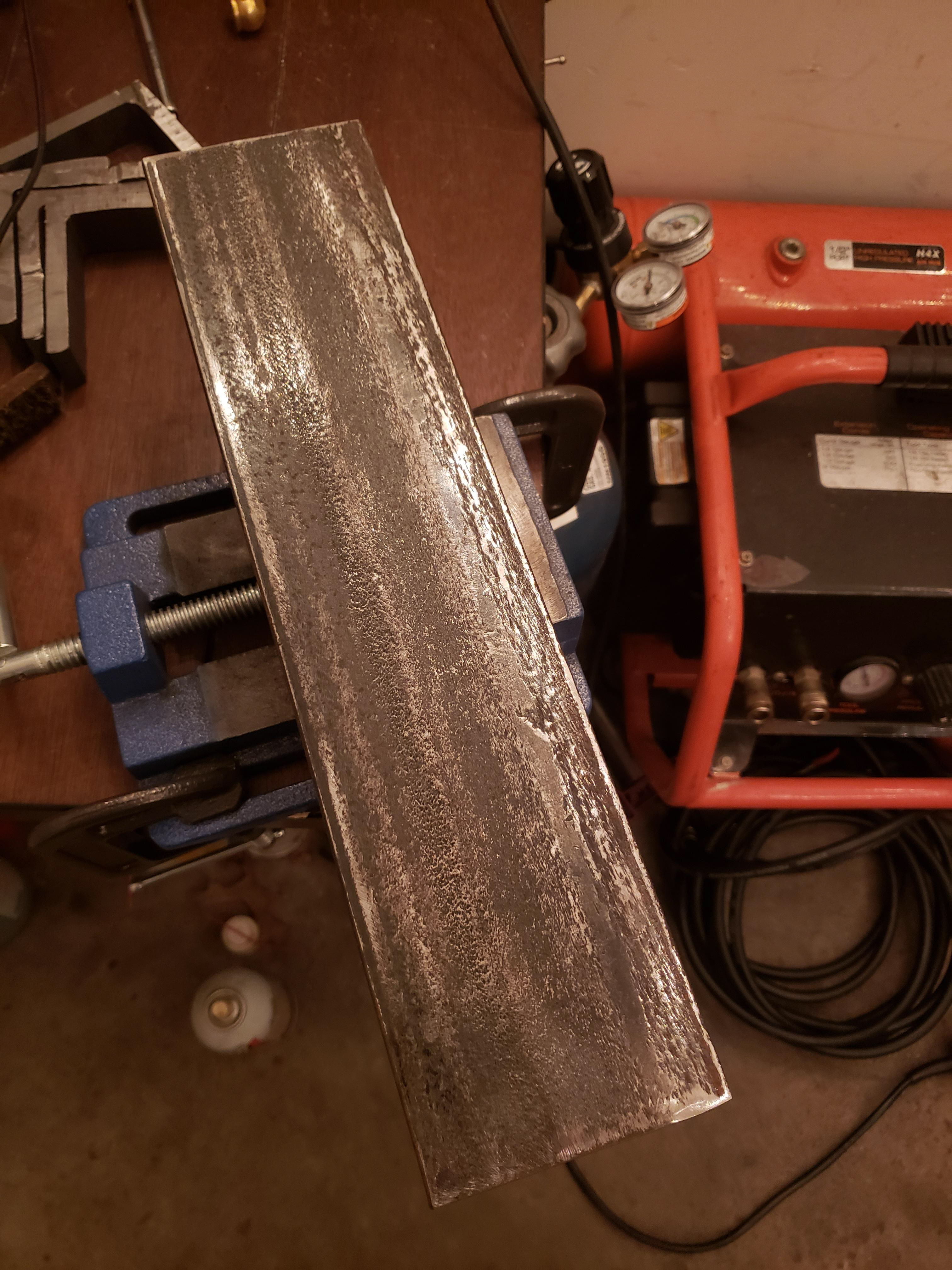
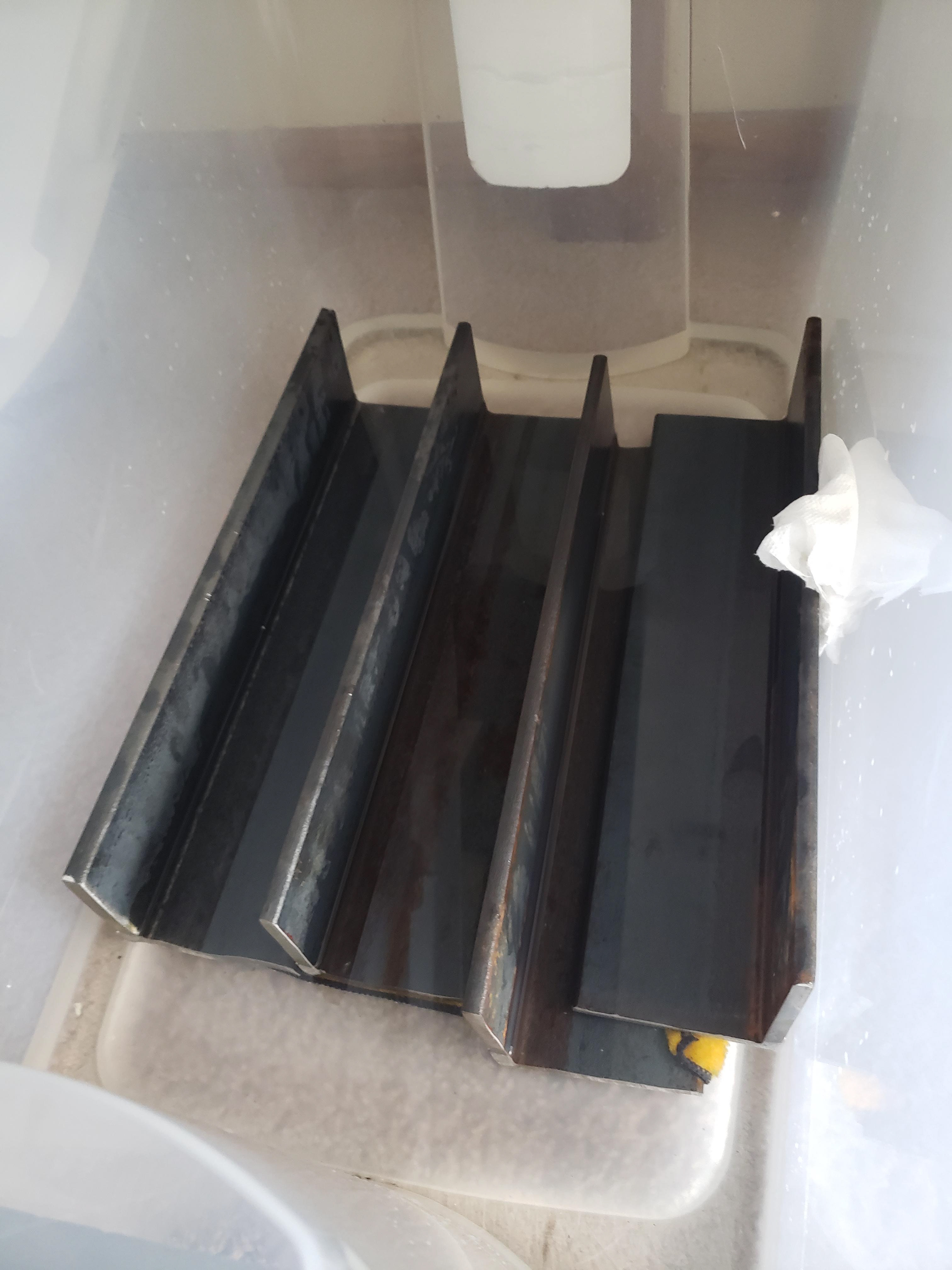
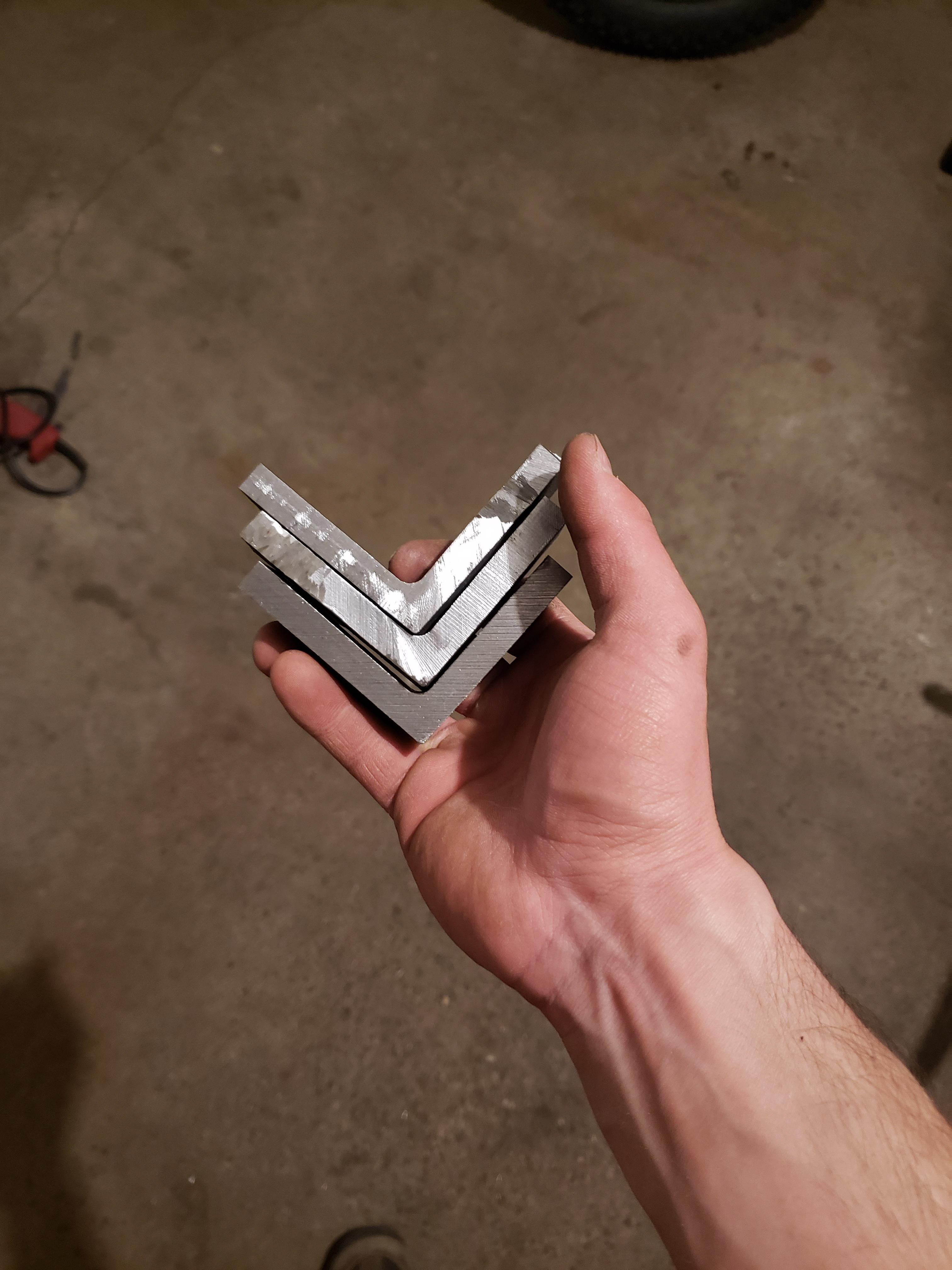
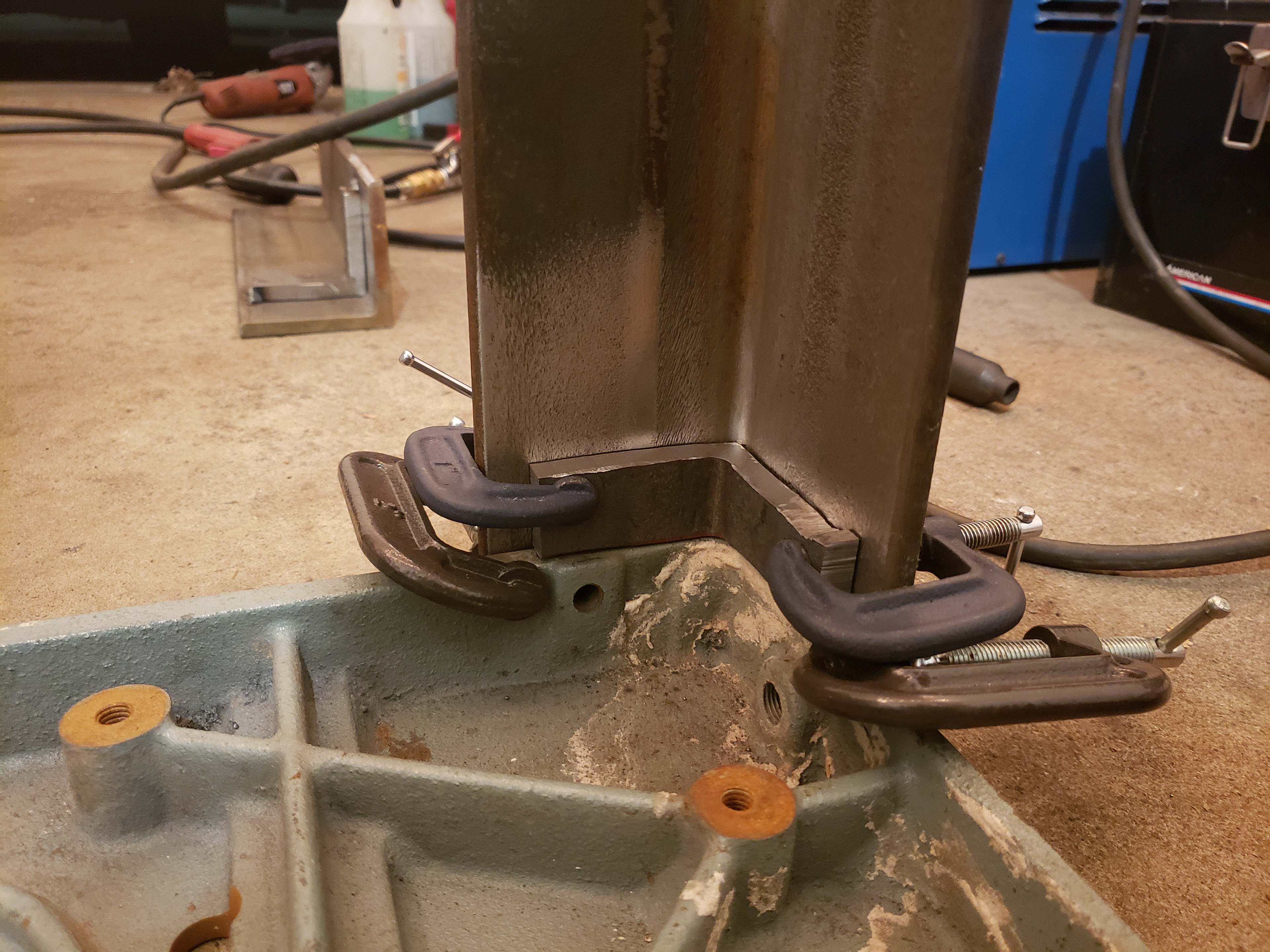
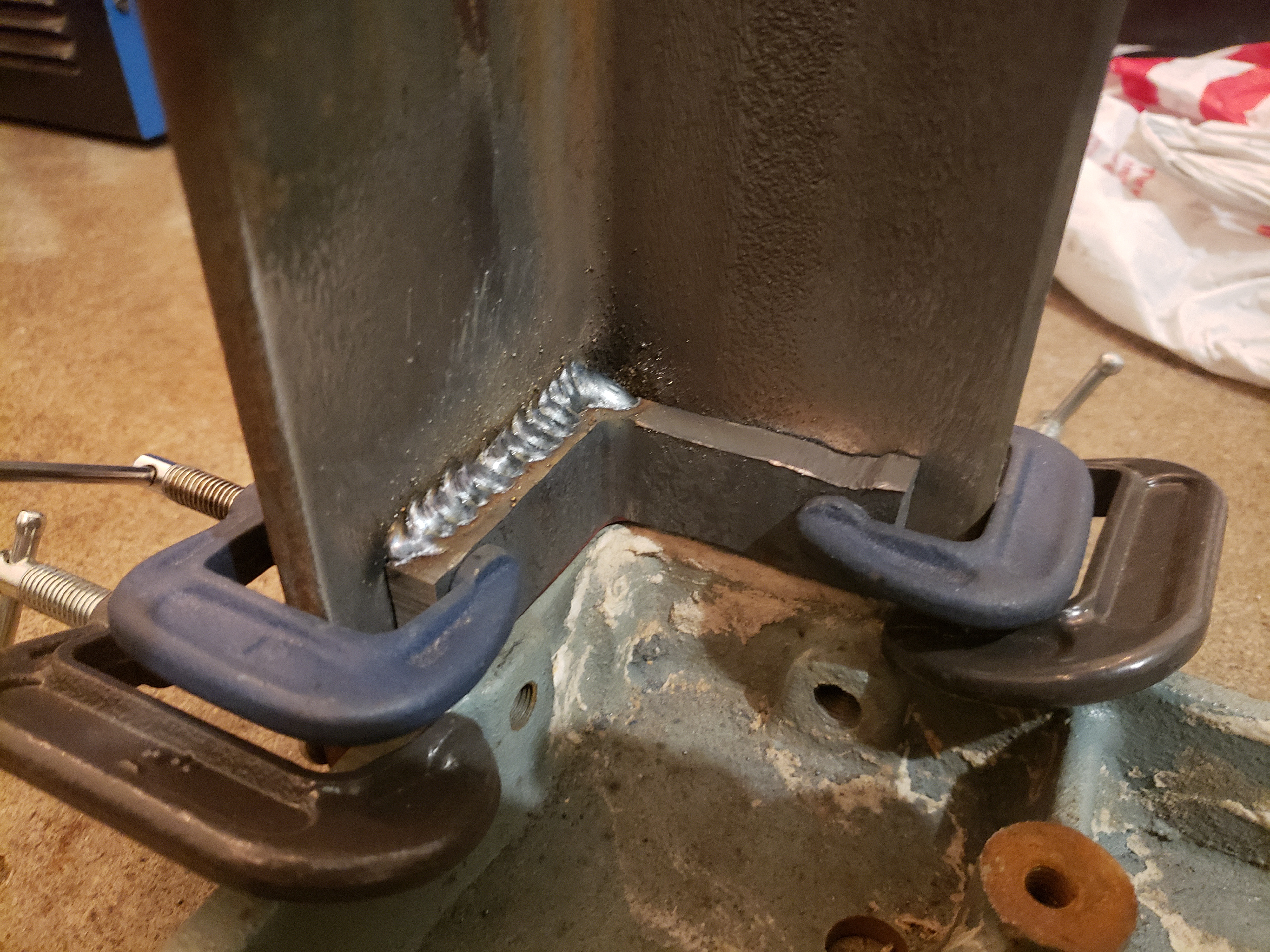
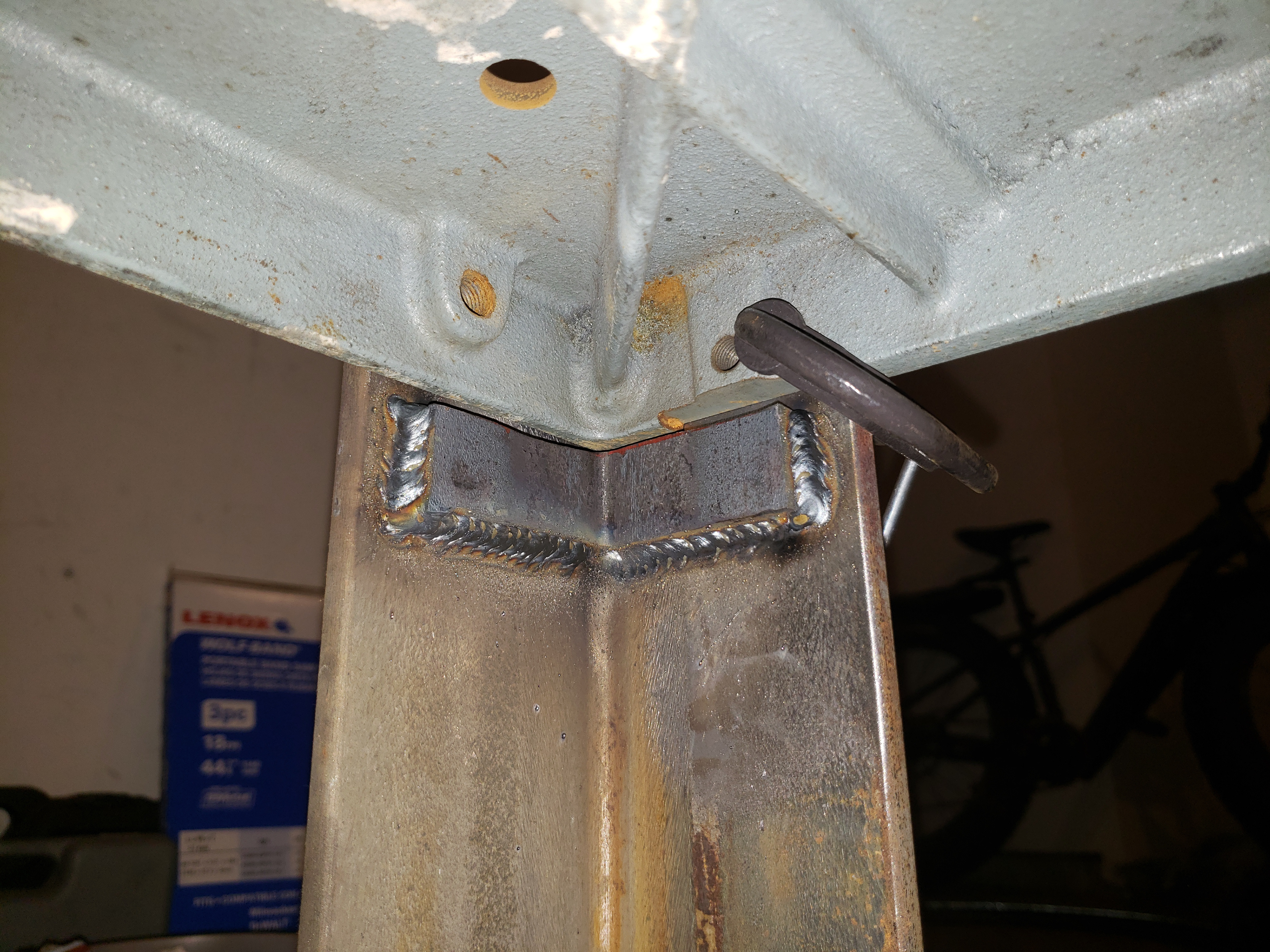
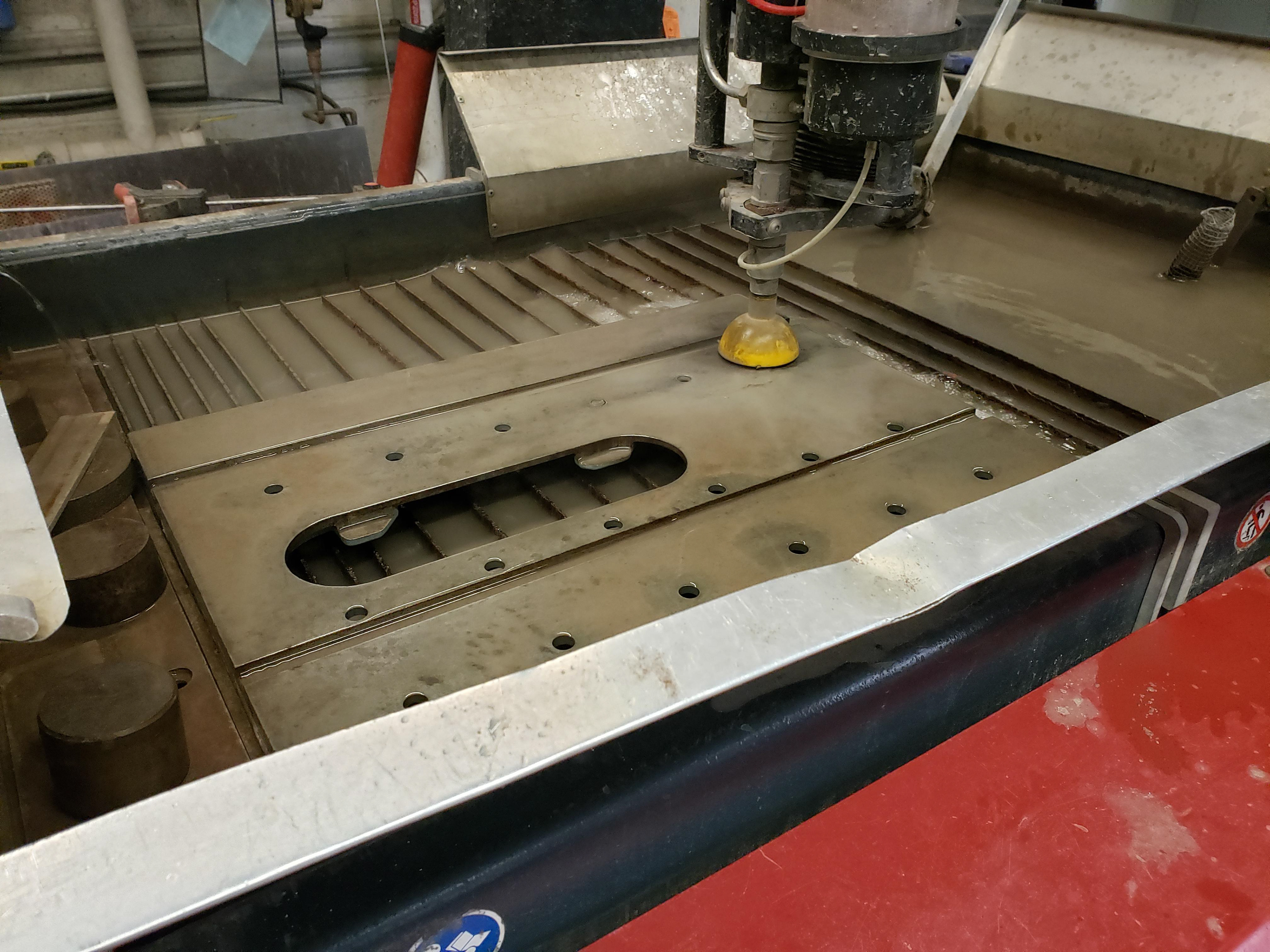
Waterjet working its magic.
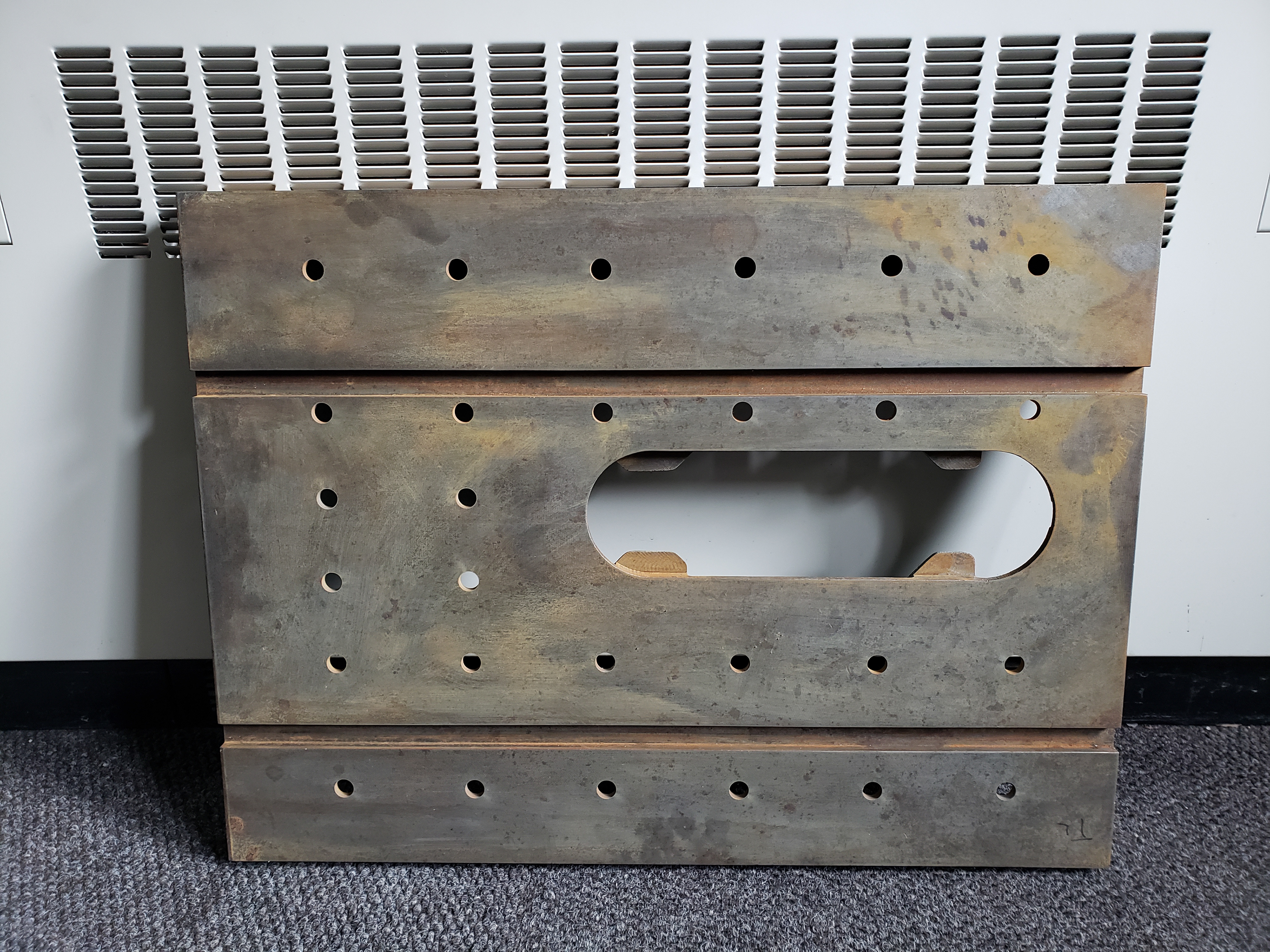
The holes are 37/64" holes, which is the drill size for 5/8-18 UNF threads.
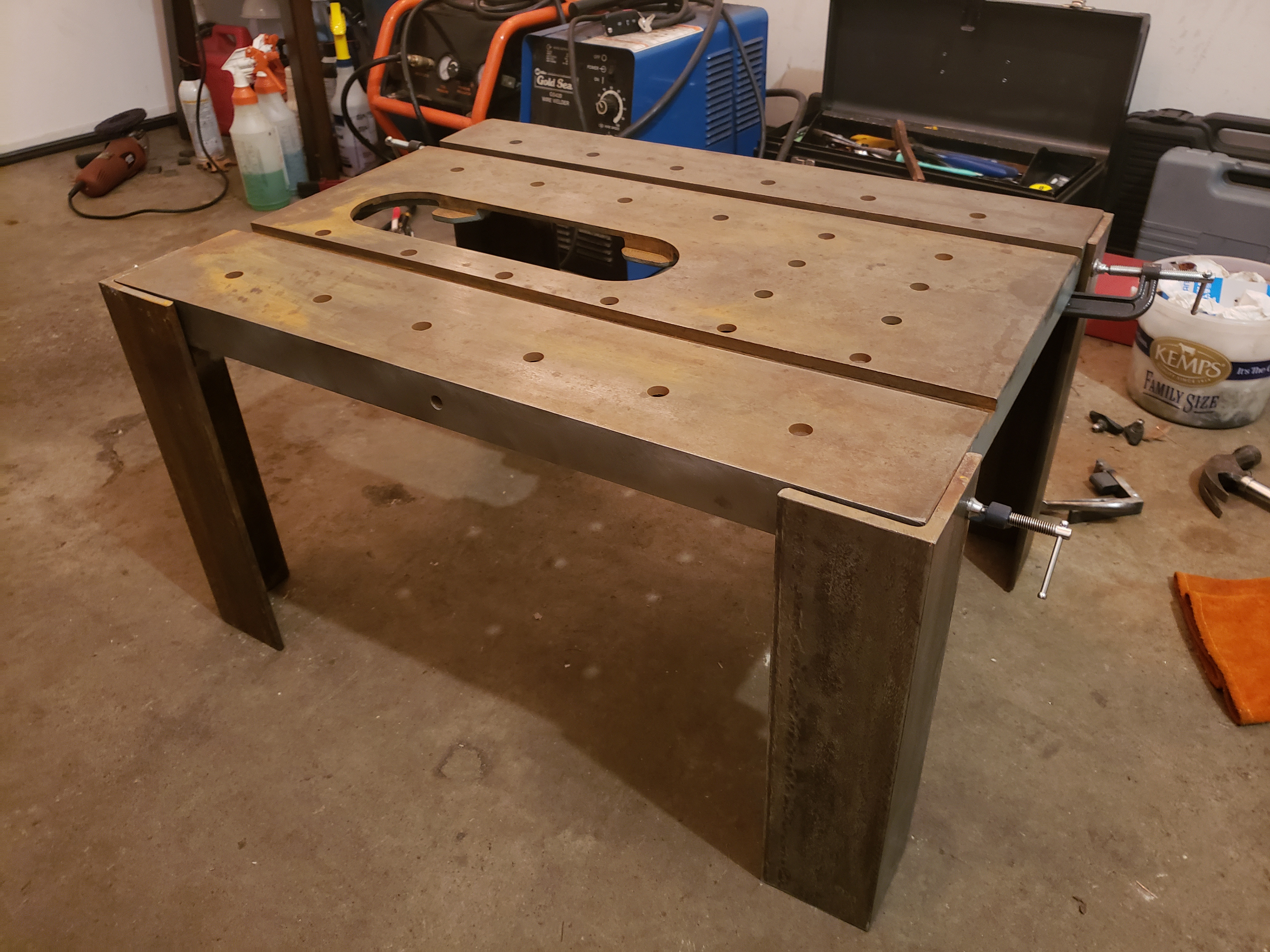
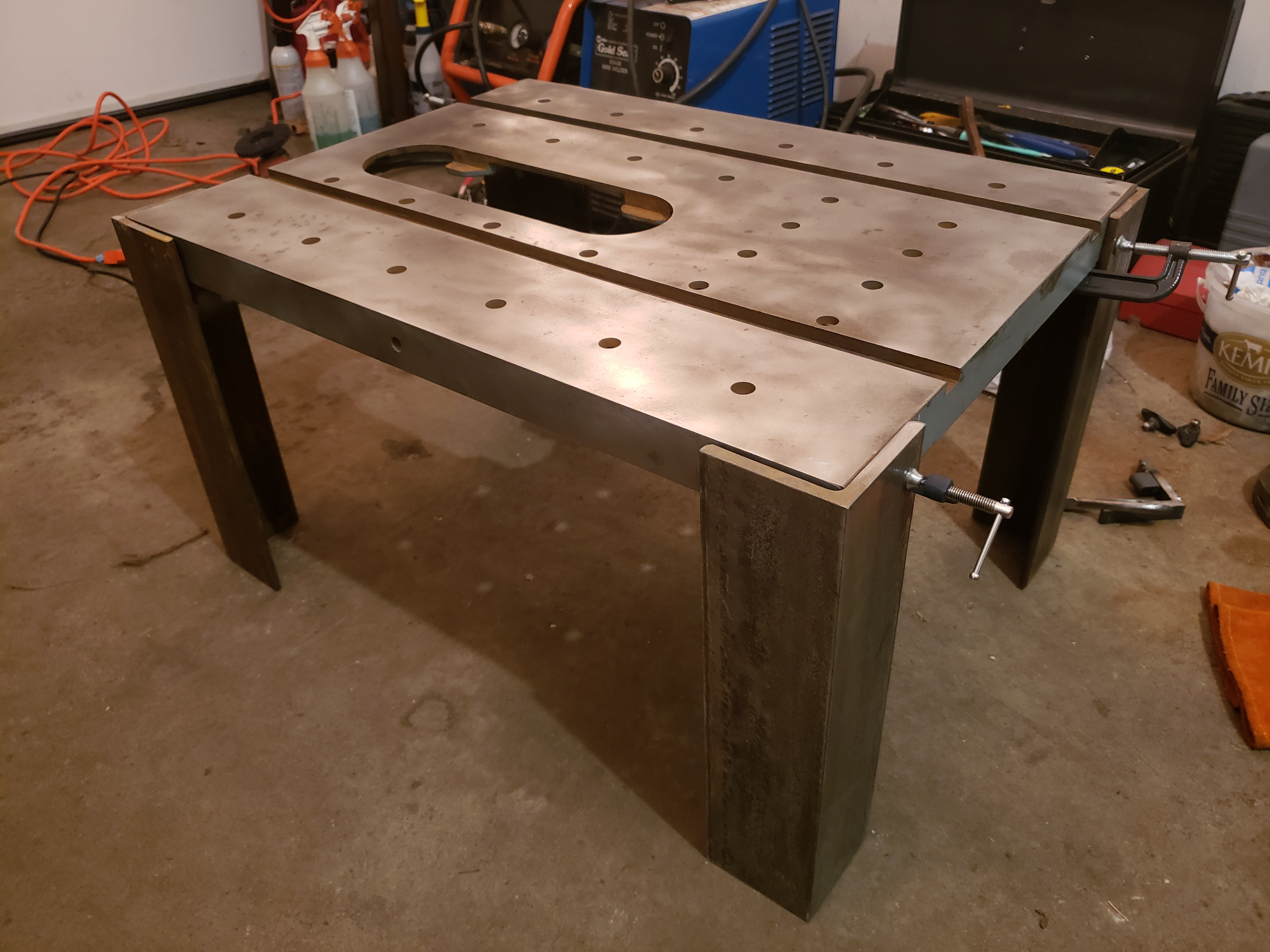
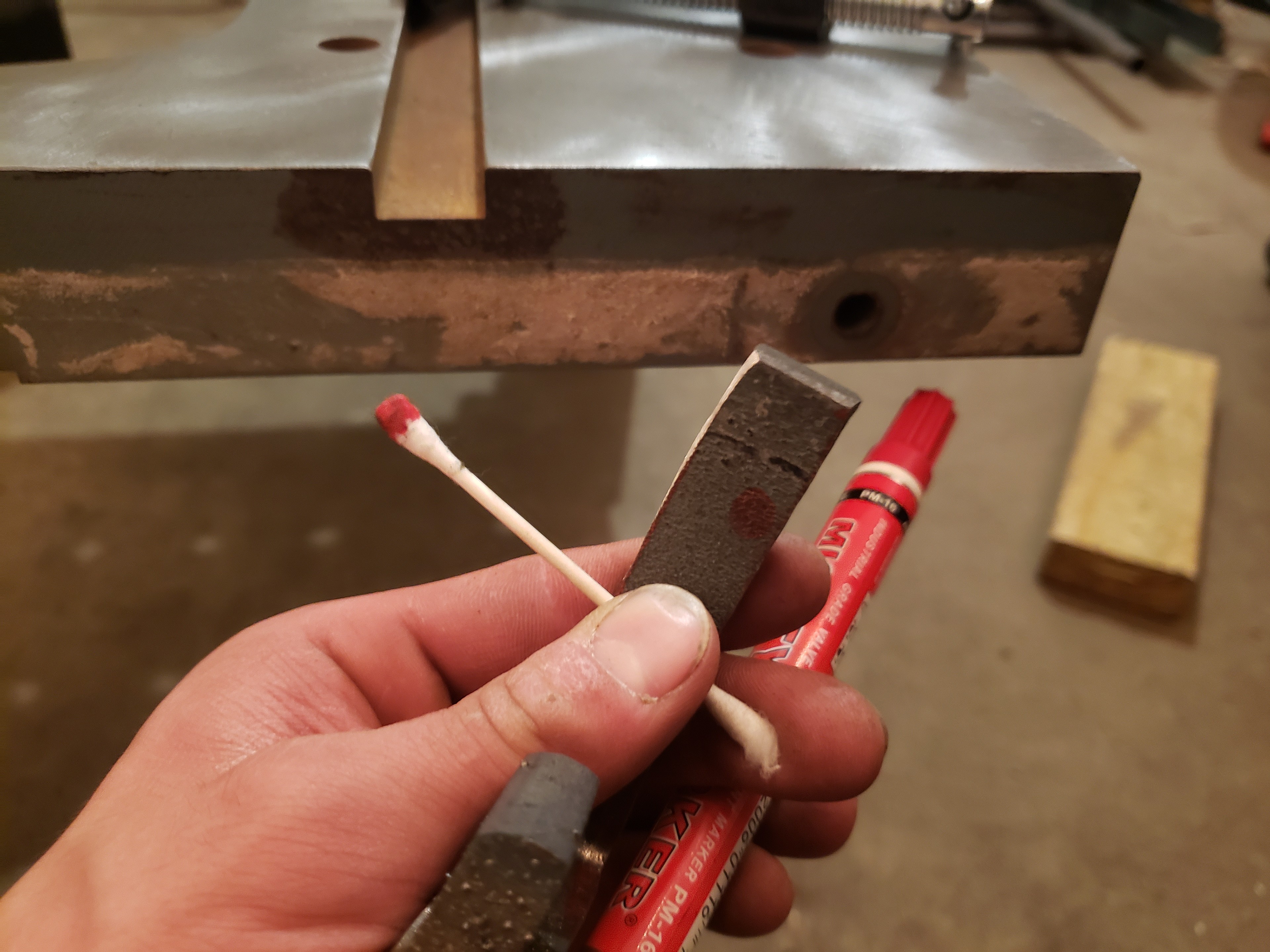
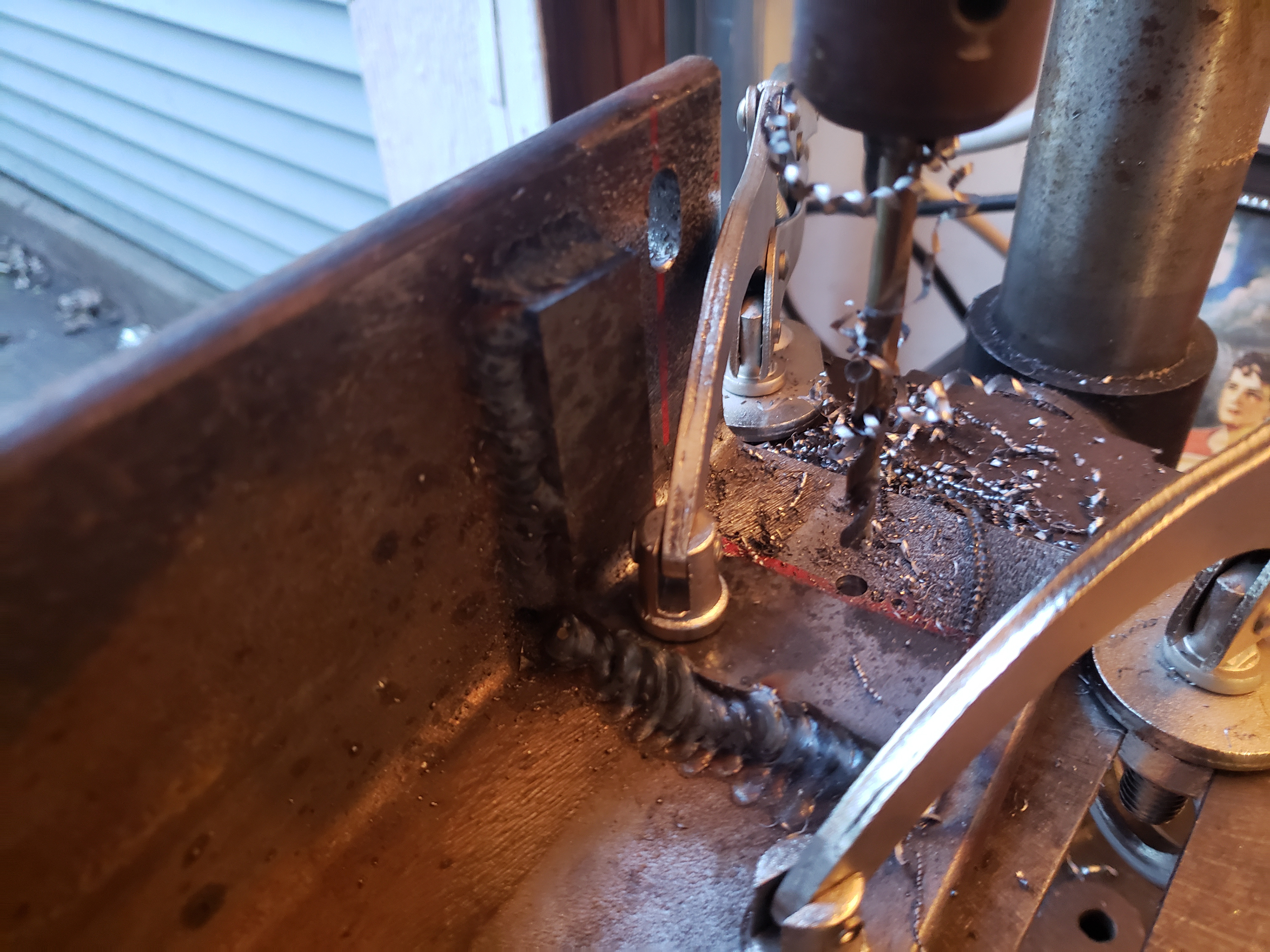

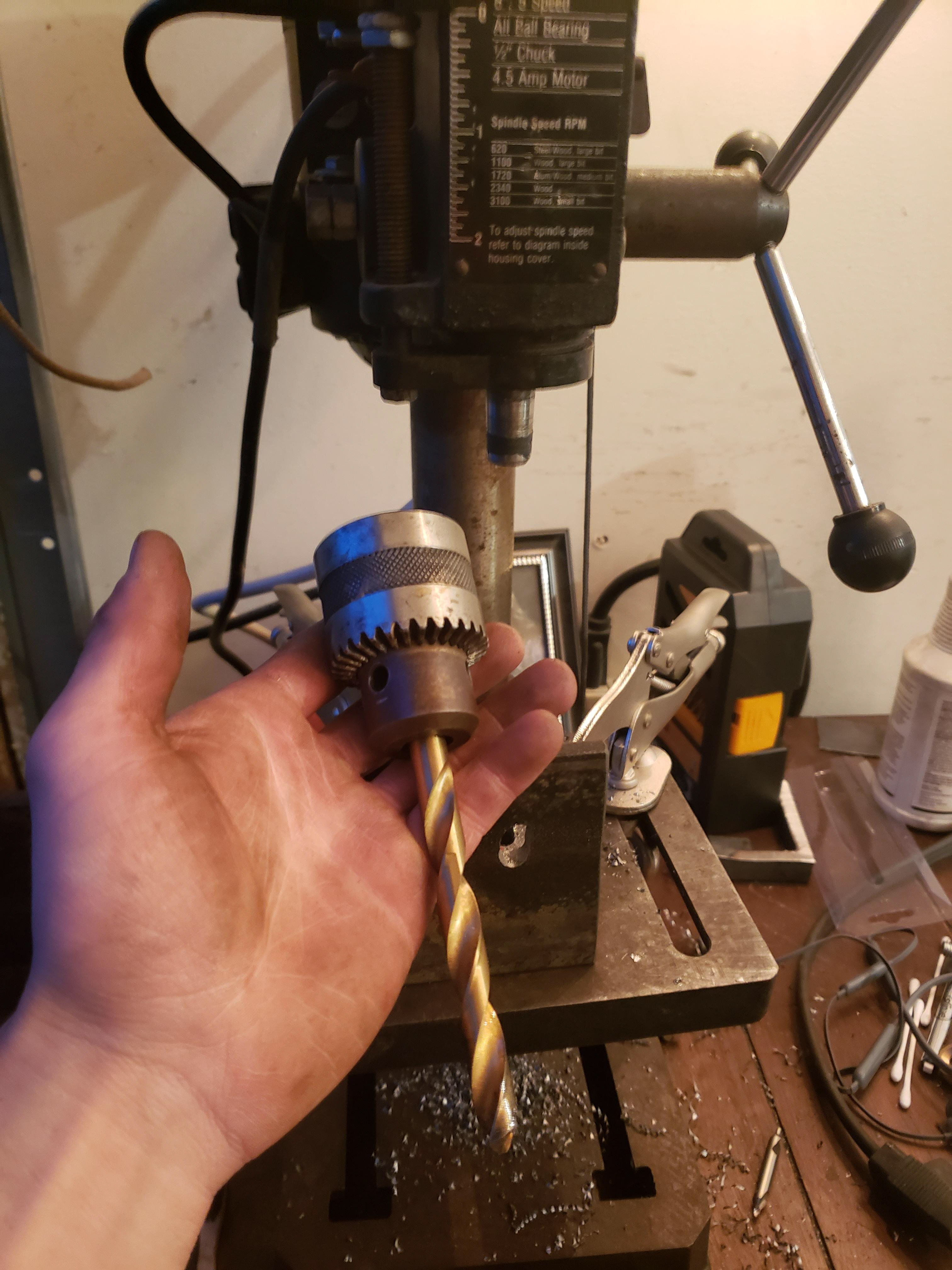
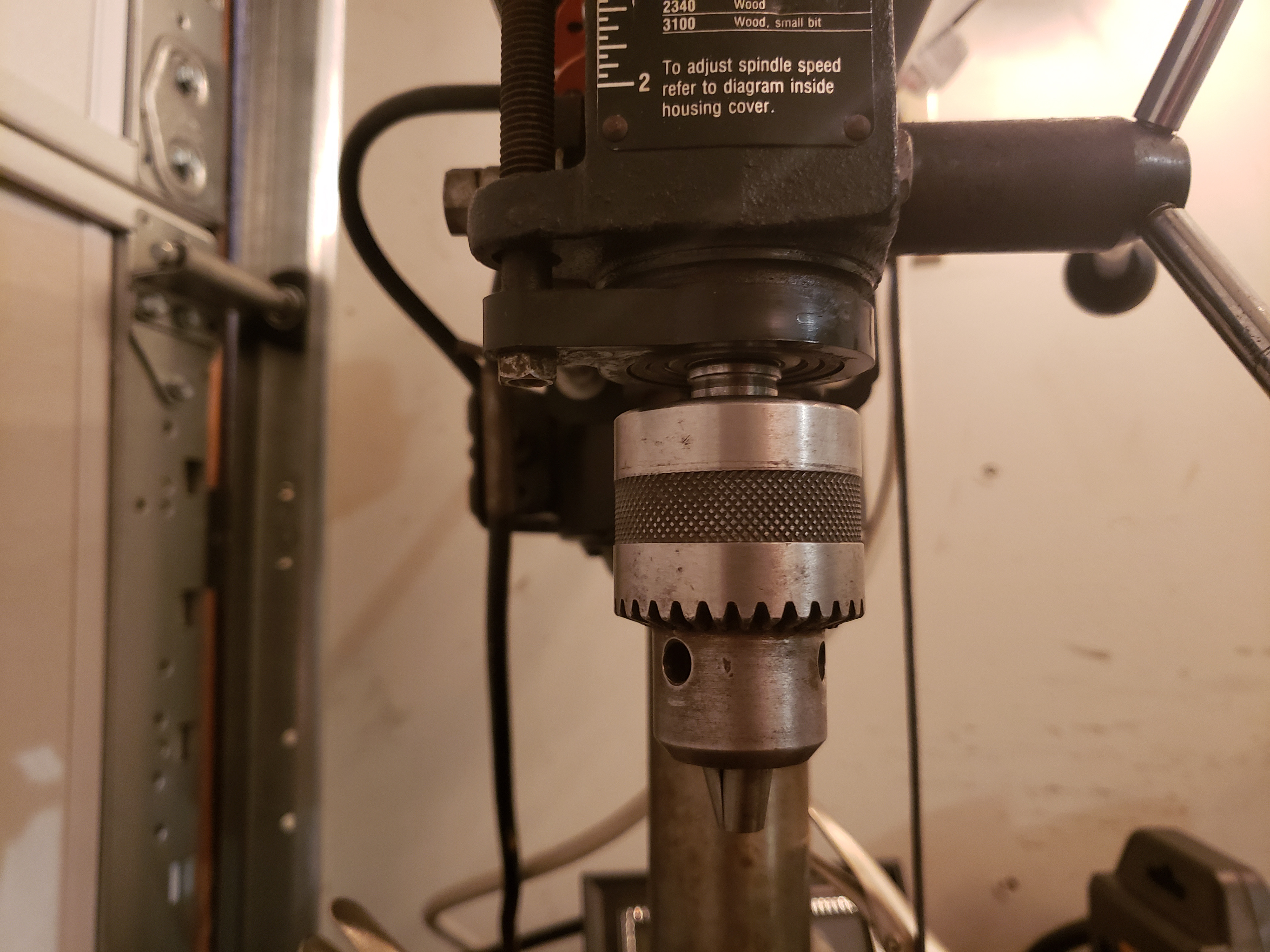
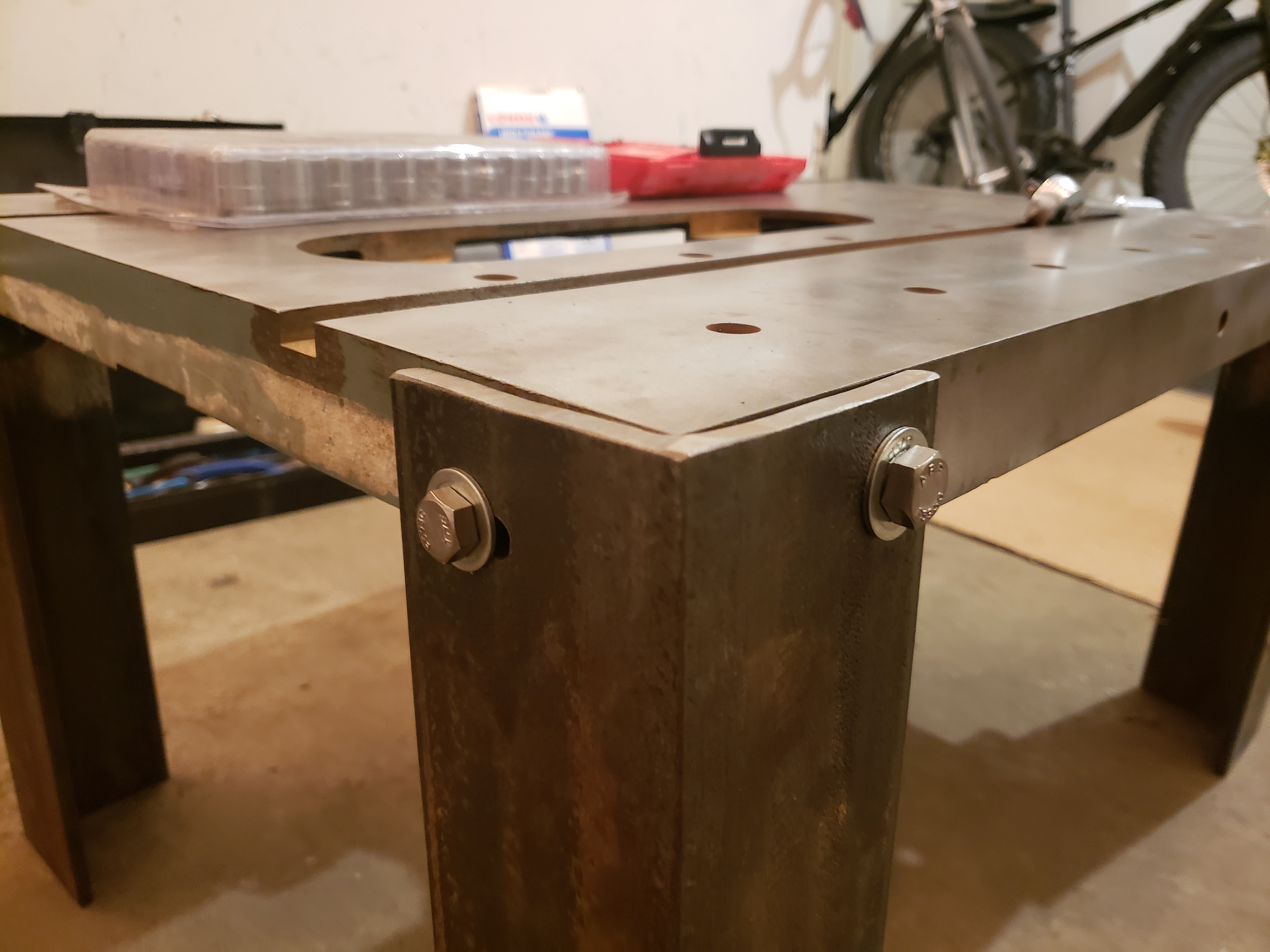
Table legs on!
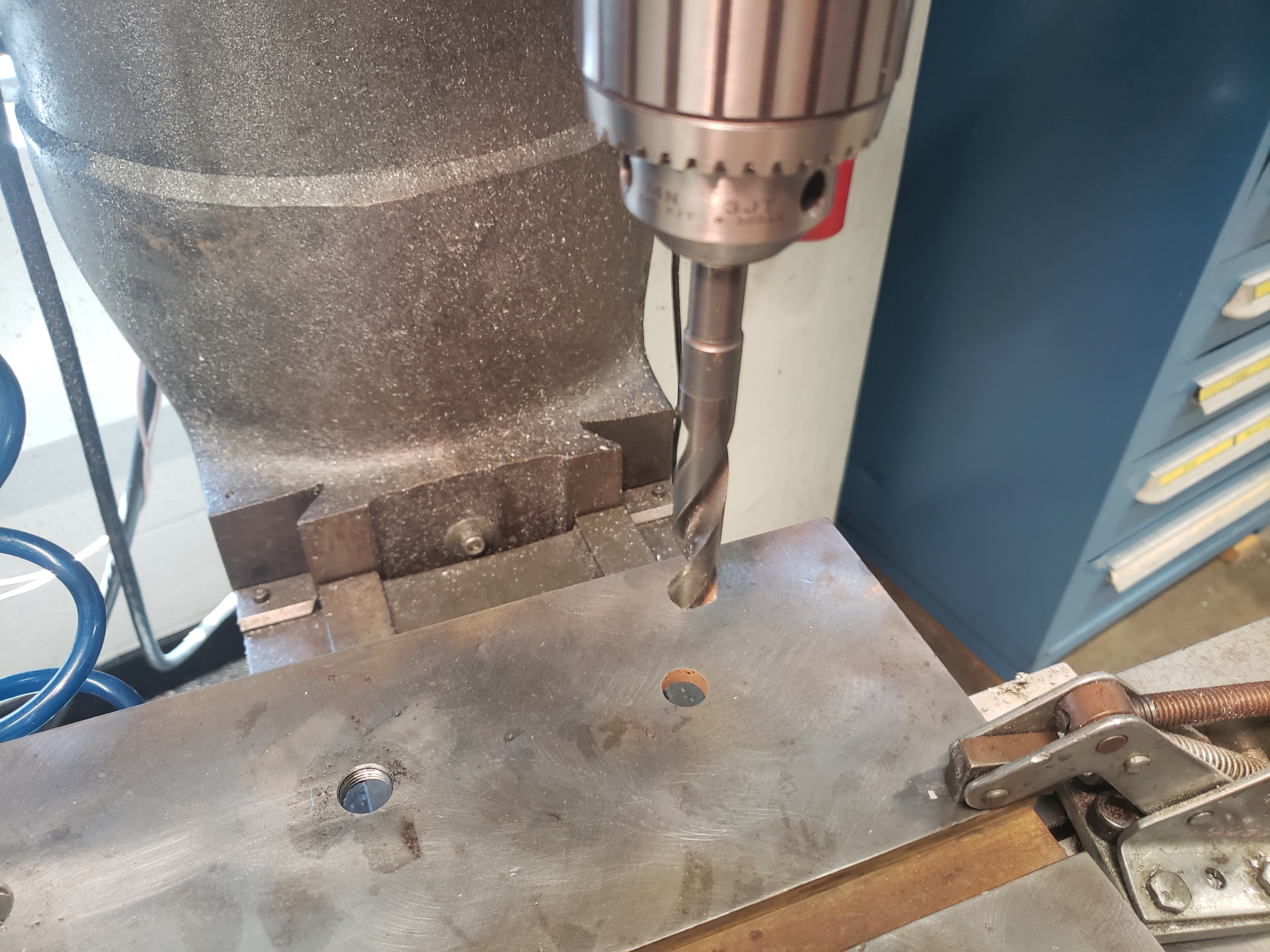
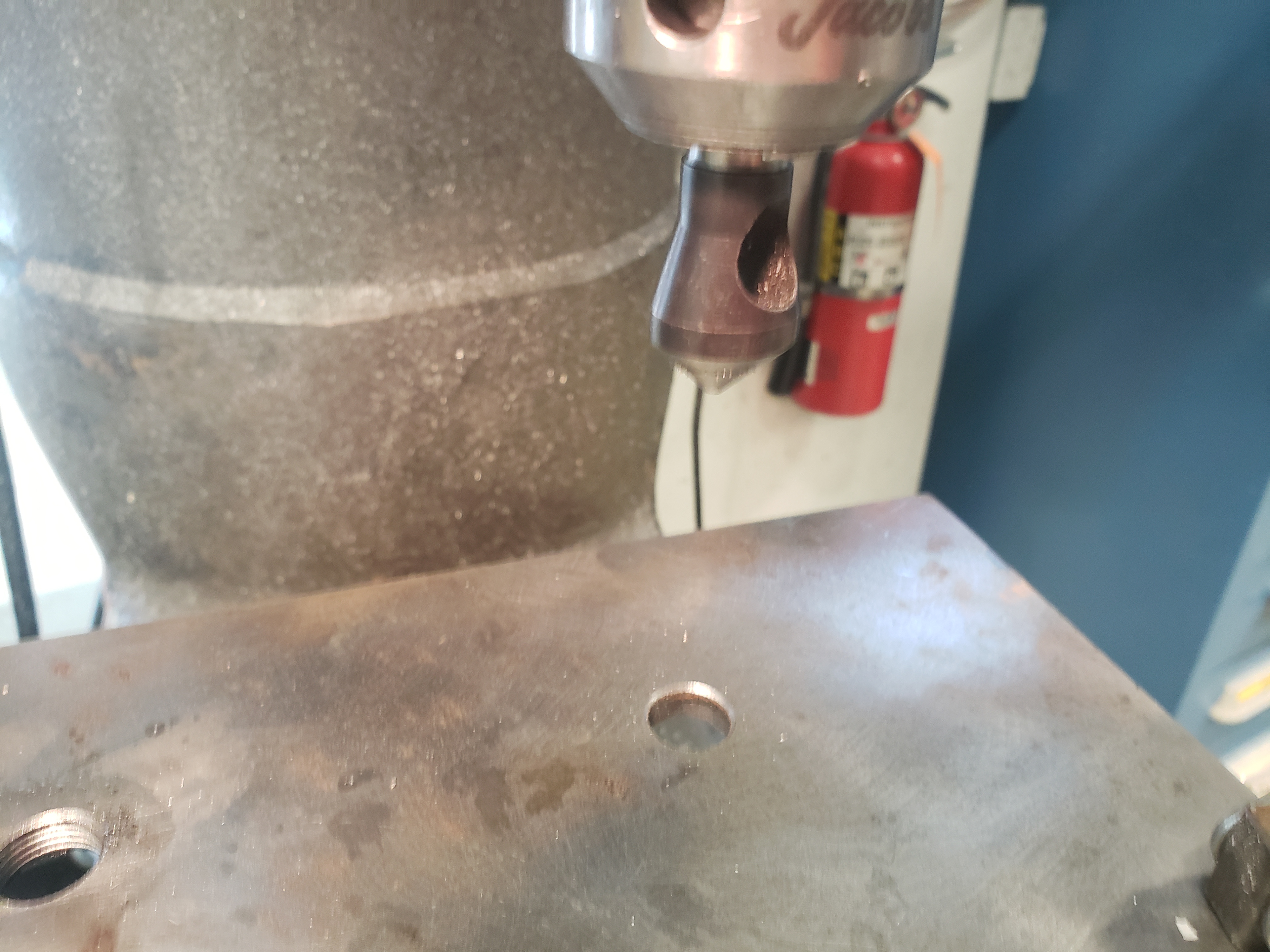
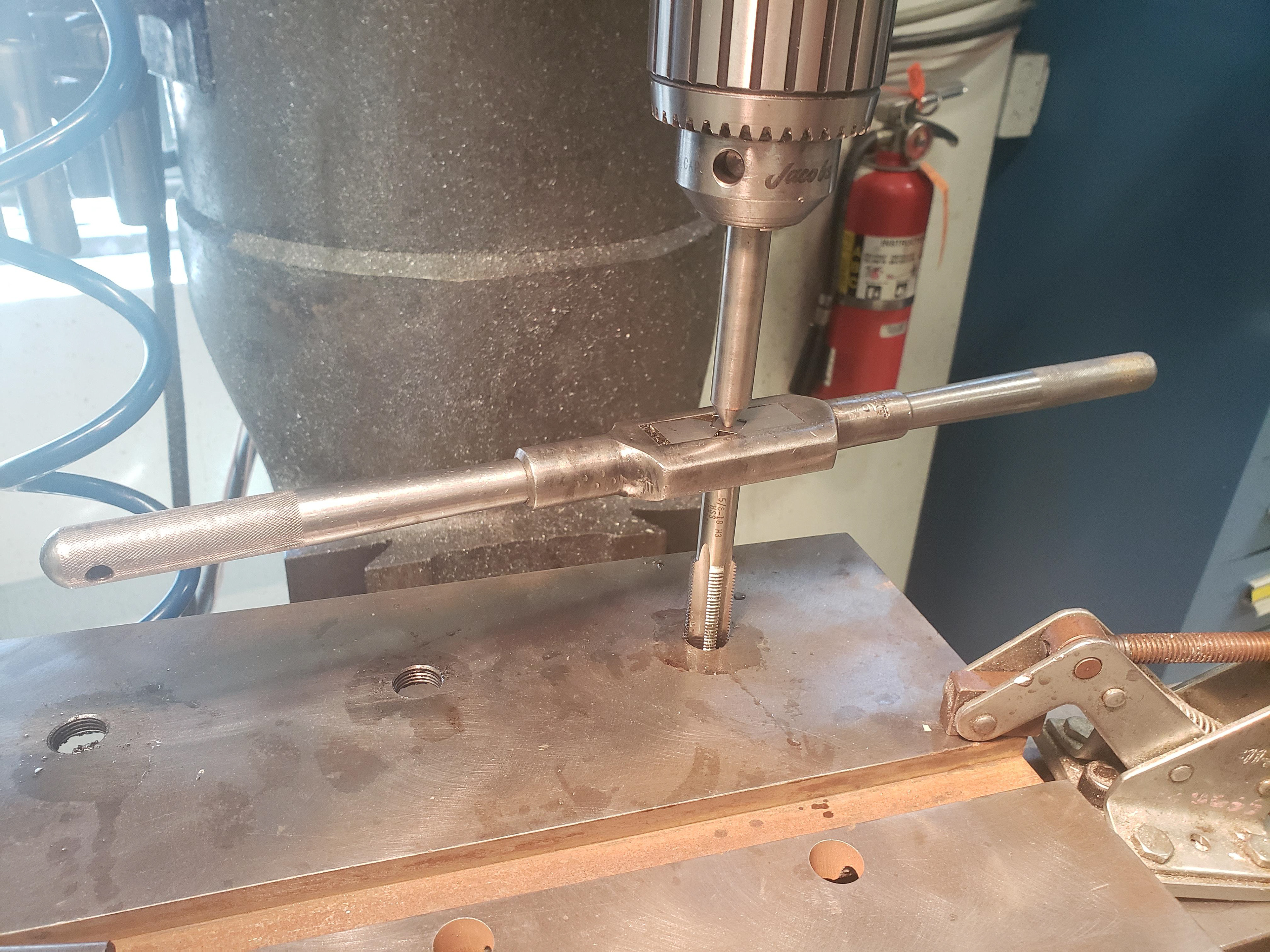
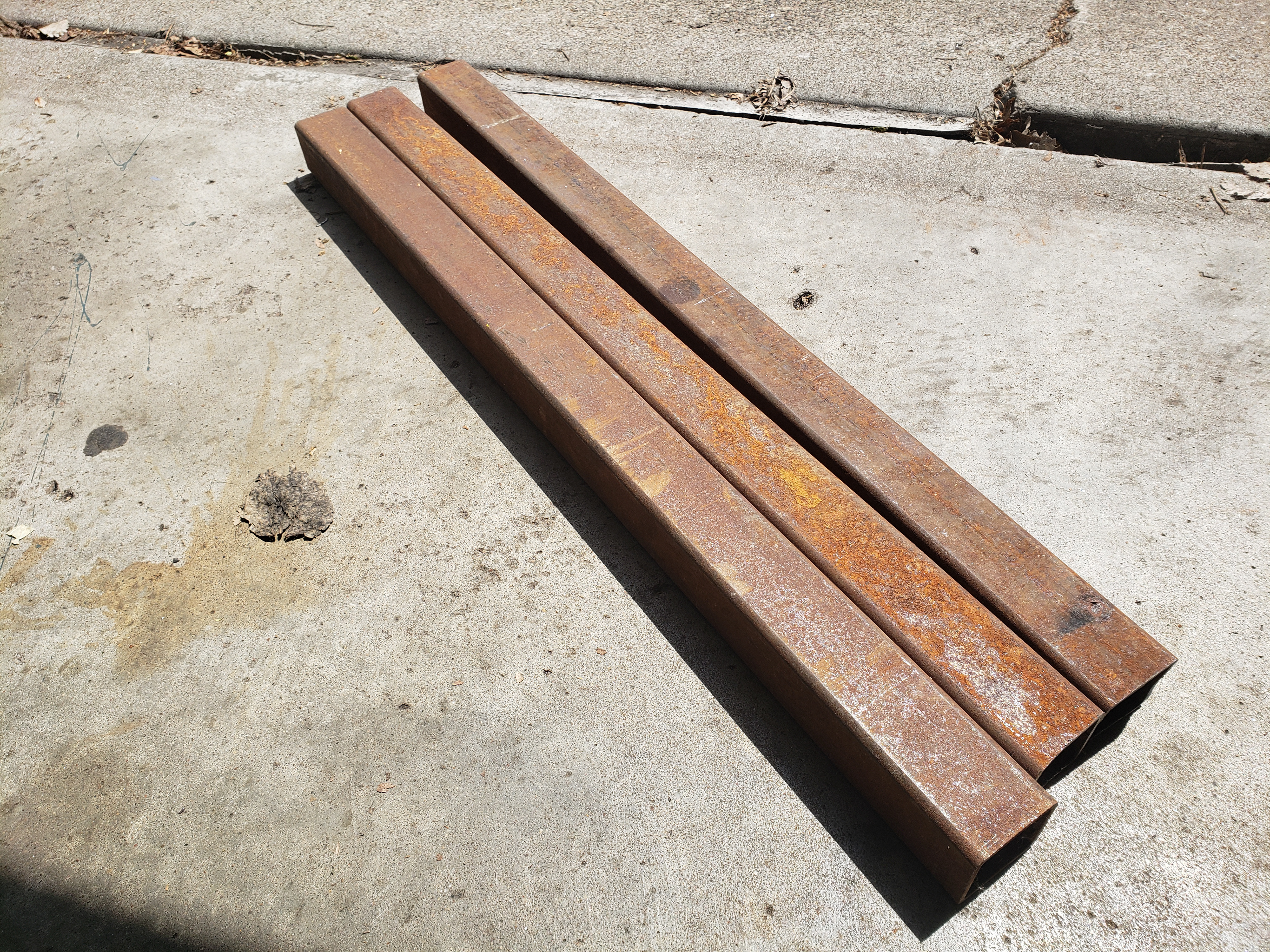
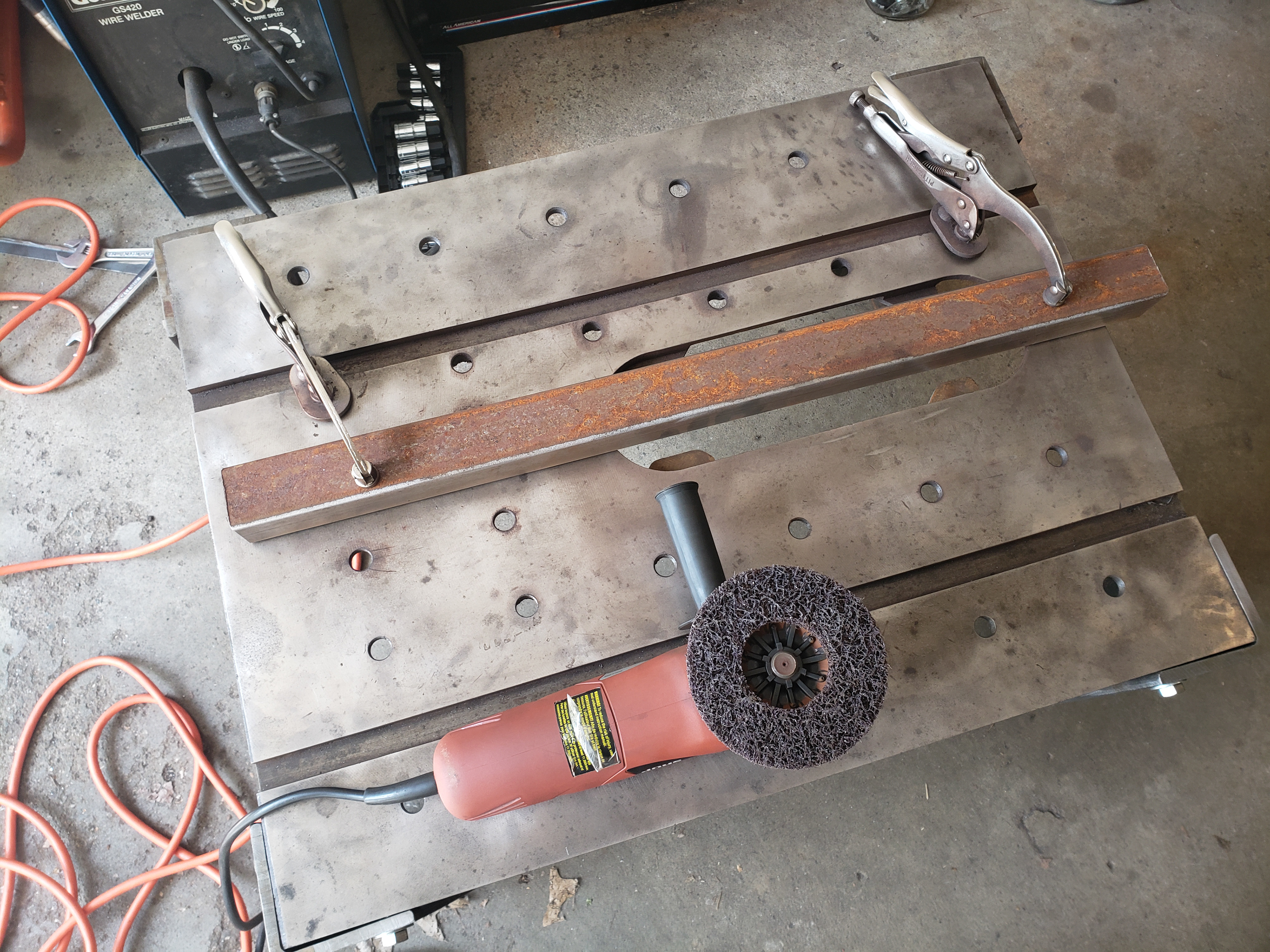
A rusty leg prior to being stripped with the Scotch-Brite Clean and Strip disc also pictured.
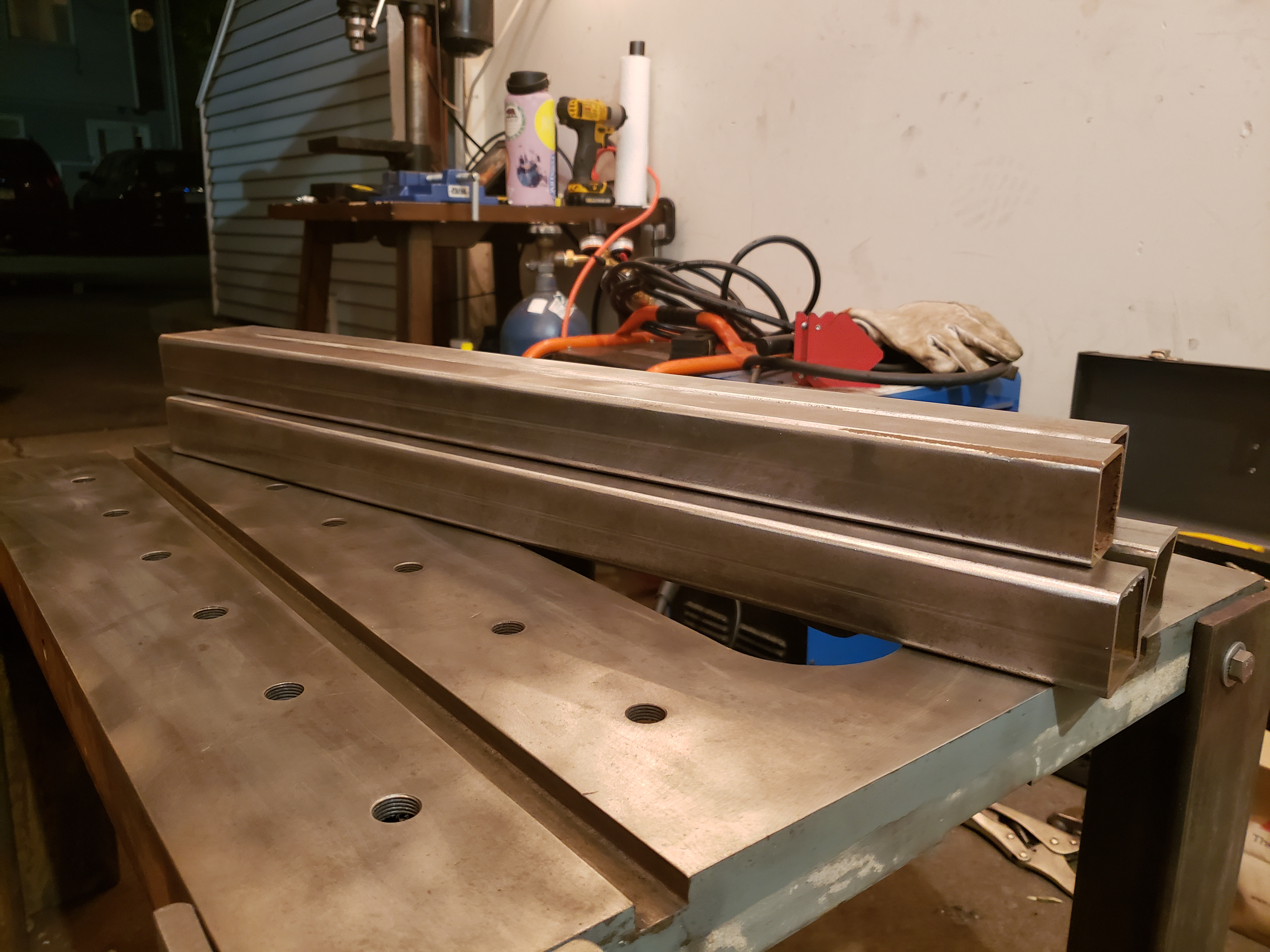
Rust free! So far, the Scotch-Brite disc has been much faster and more importantly more durable than the flap discs at removing rust and mill scale.
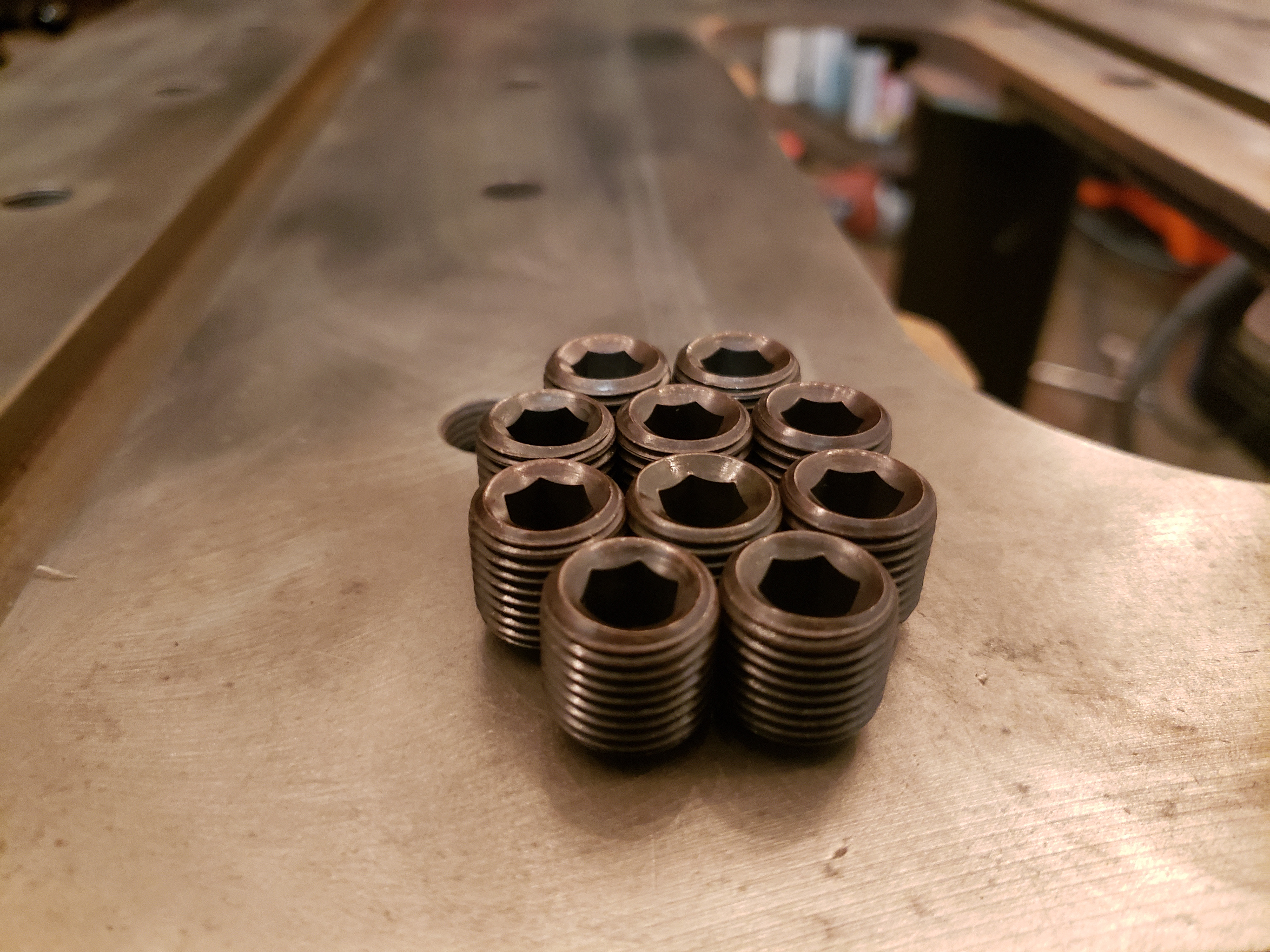
Set screws
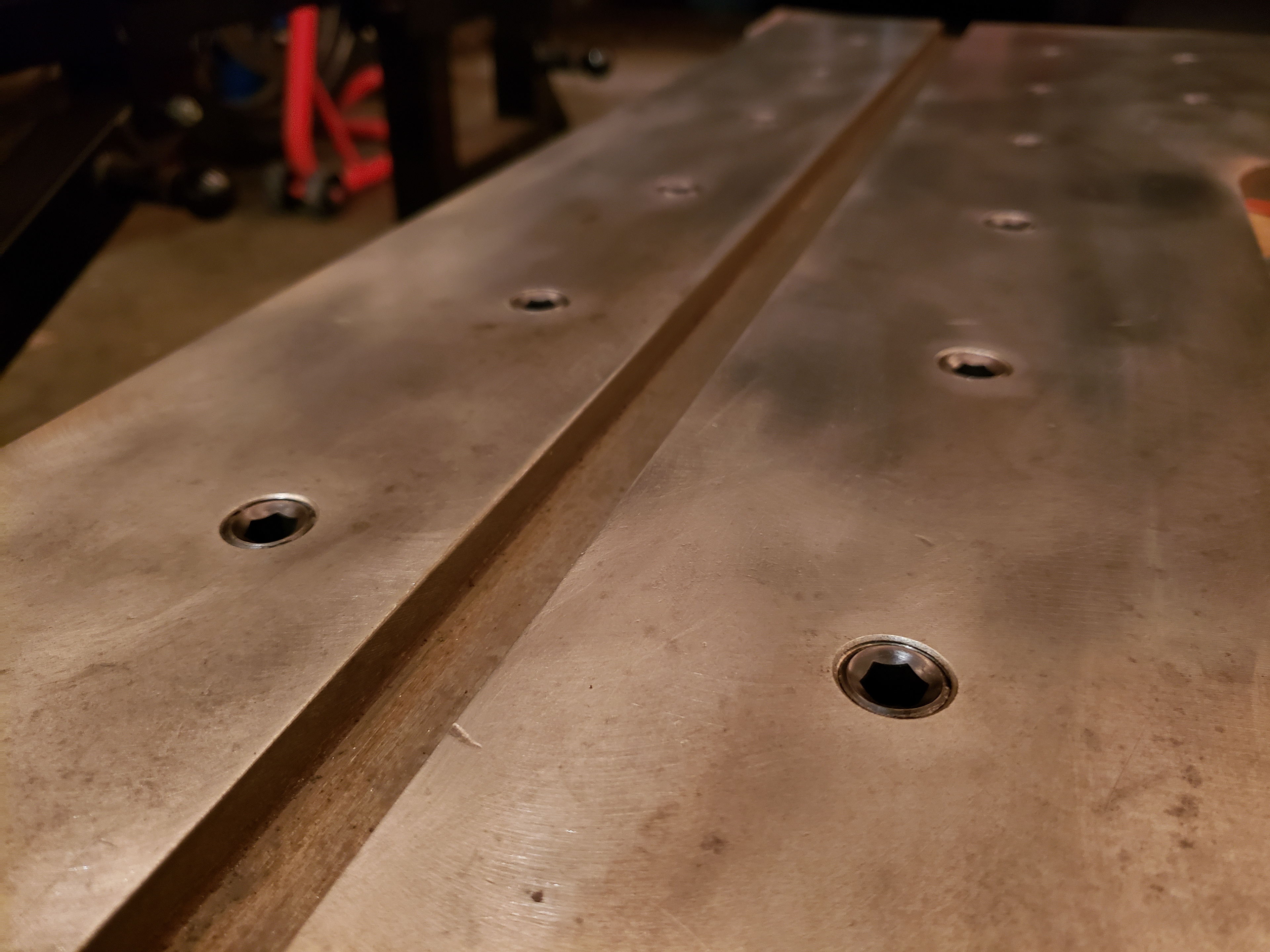
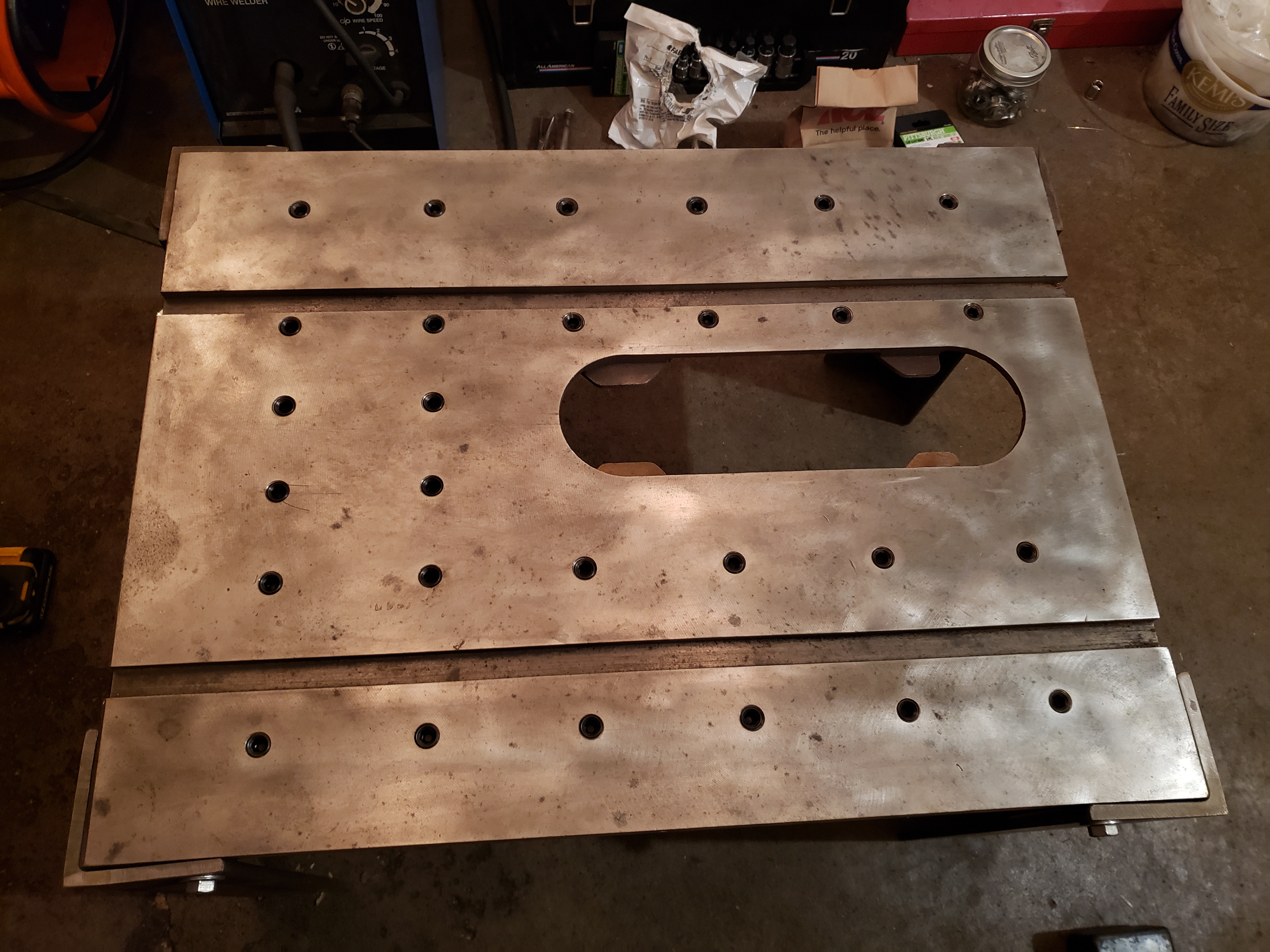
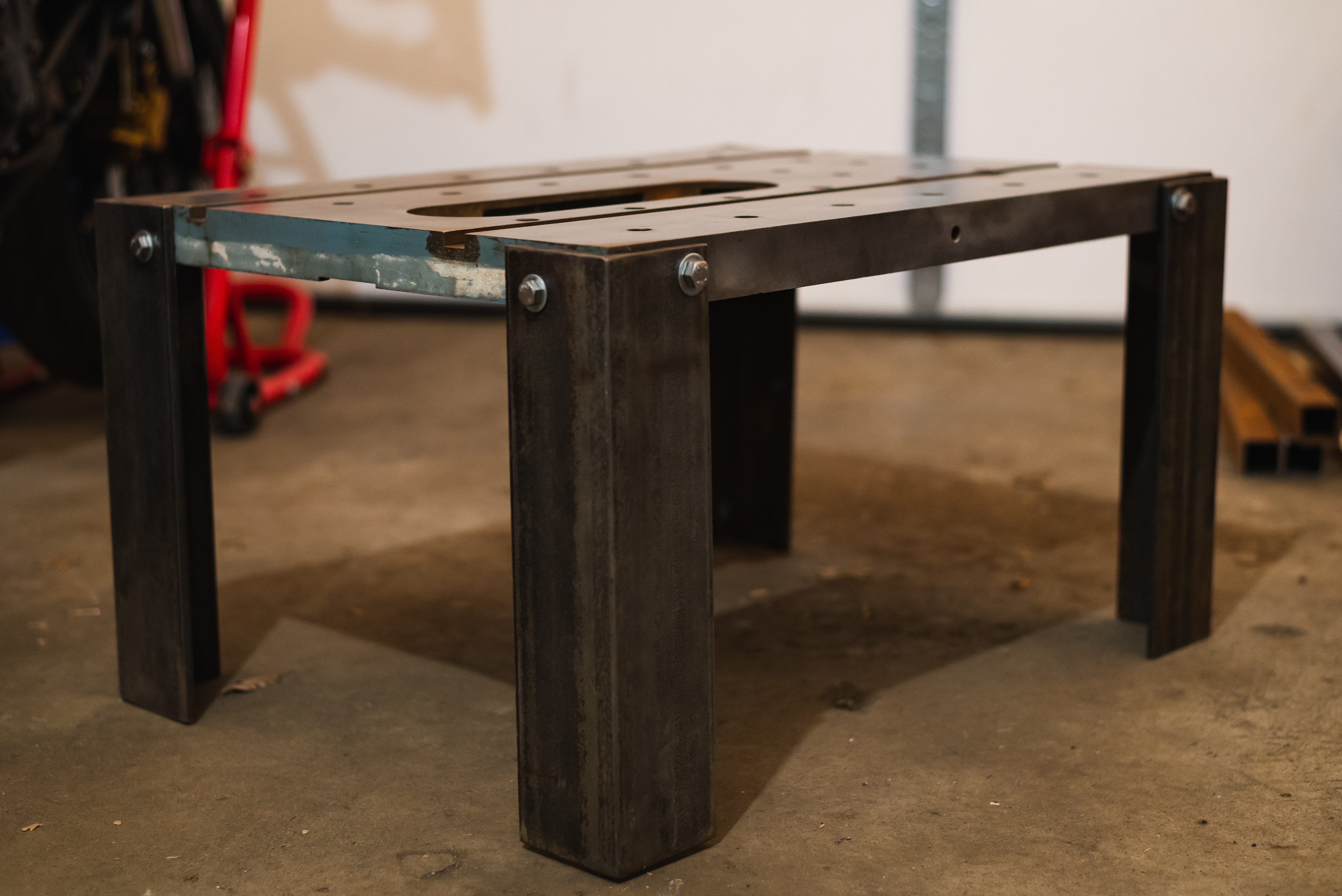
A milestone in the workbench's progress!
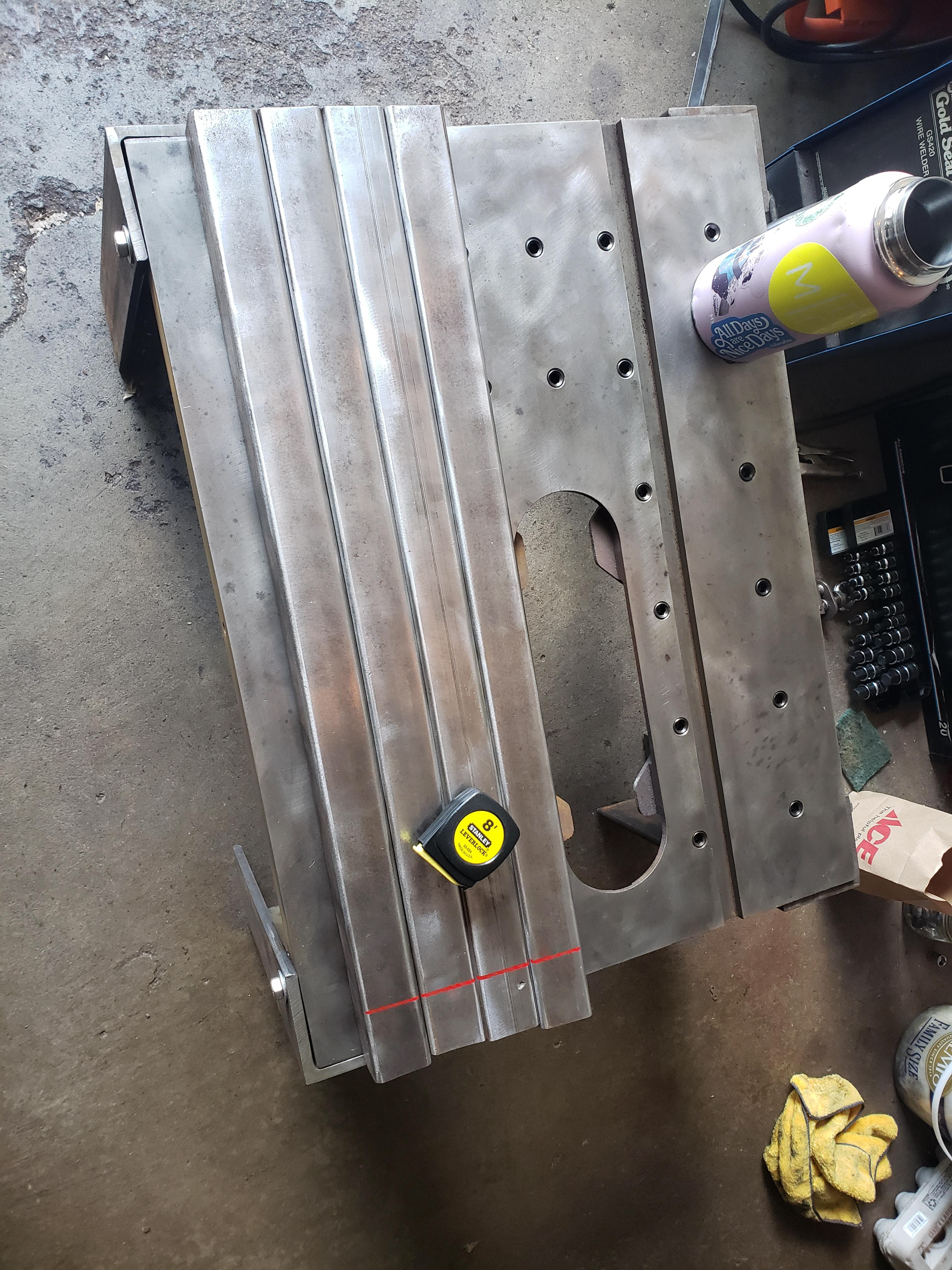
Cutting the leg lowers.
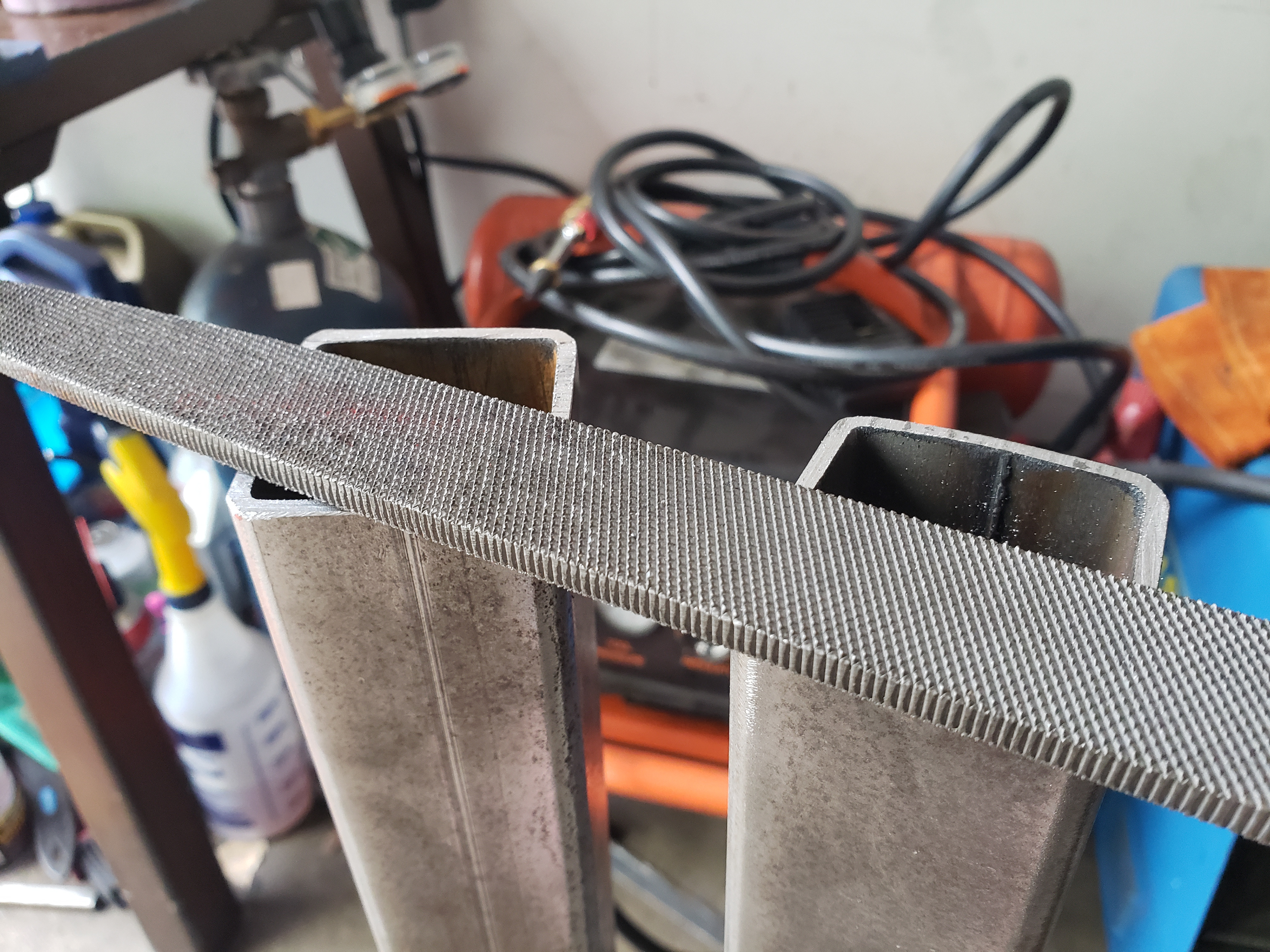
Filing the cuts smooth!
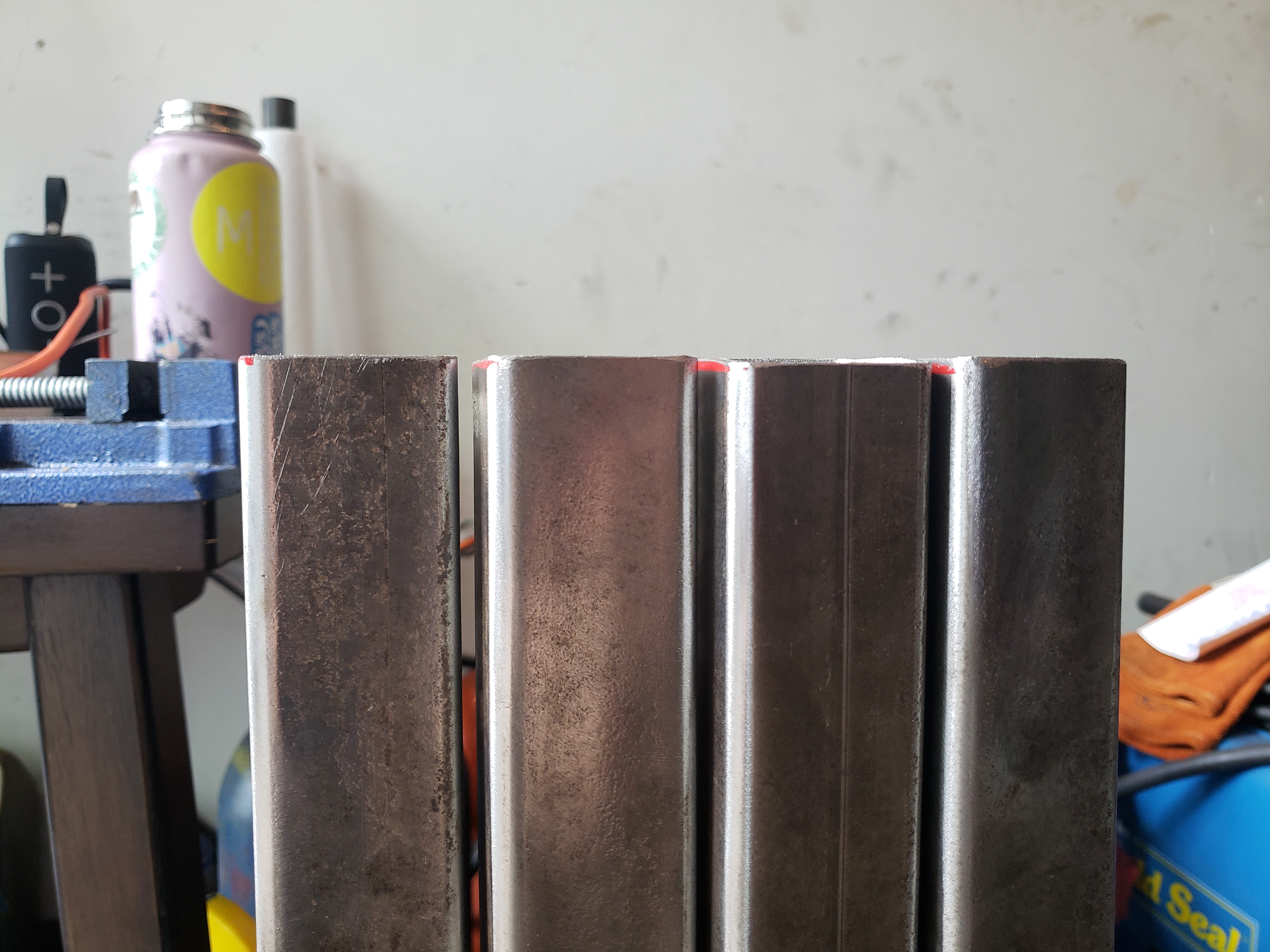
Nice and even.
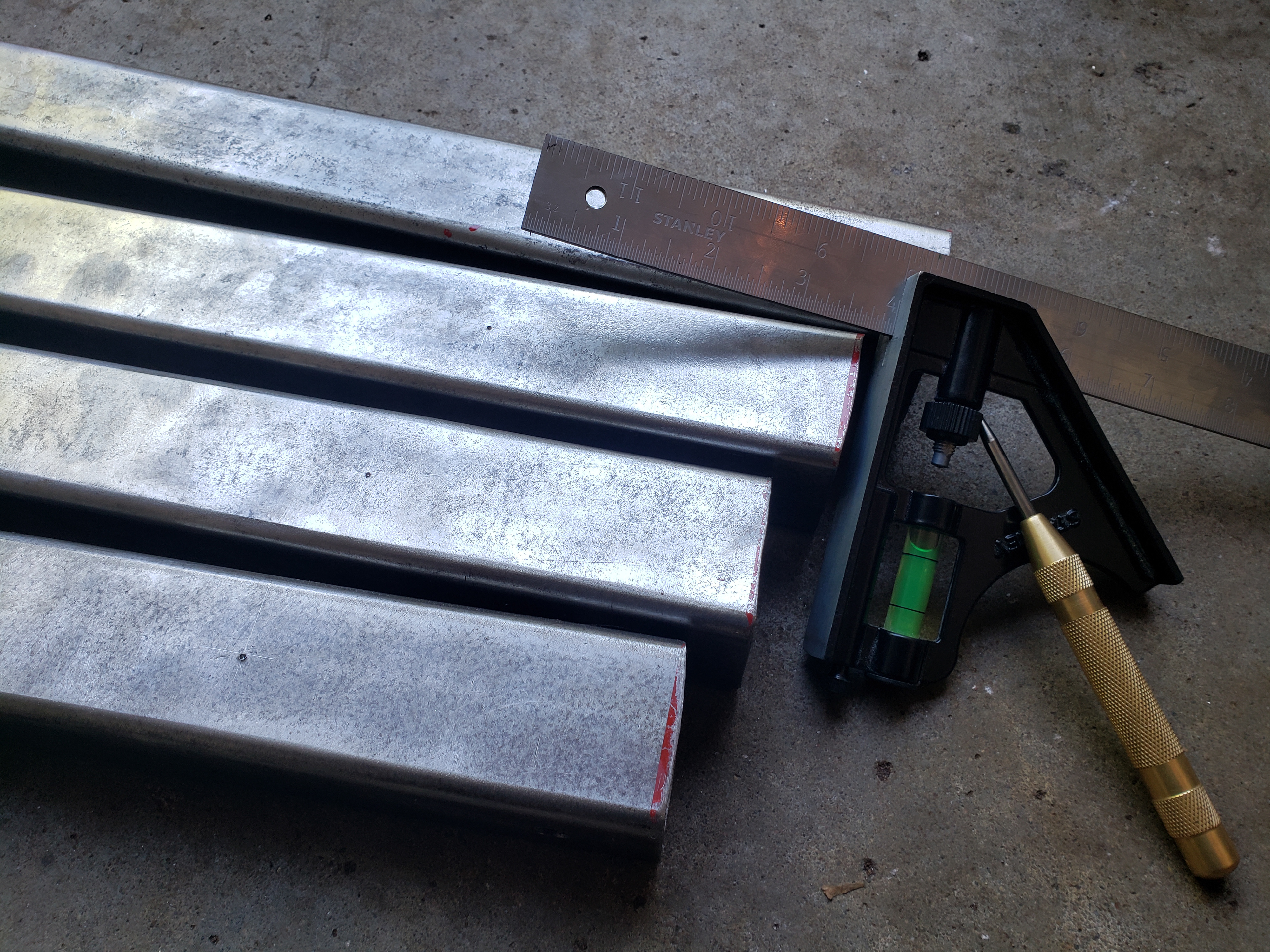
Making sure the holes align perfectly with the uppers.

Holes drilled in upper.
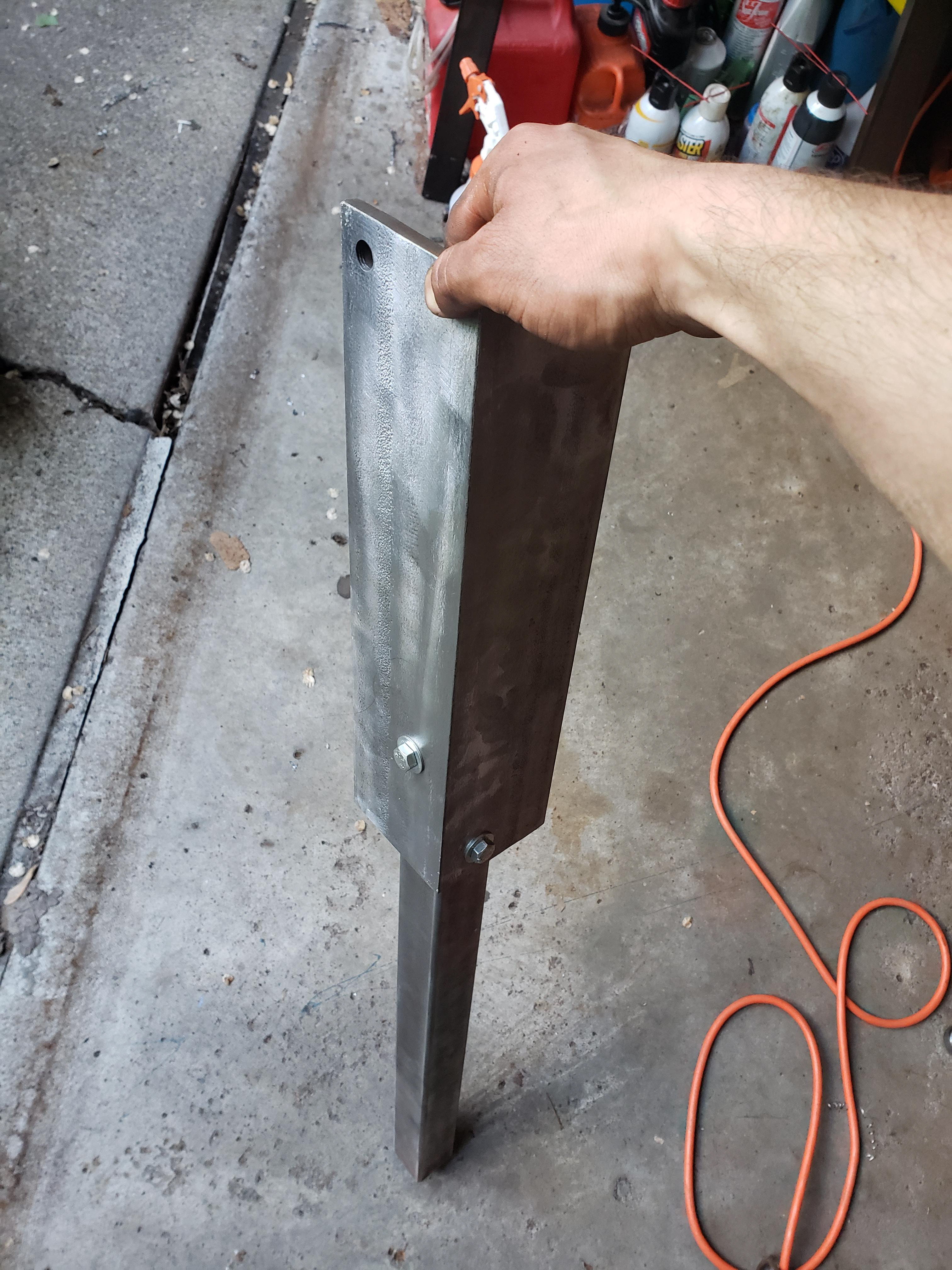
One leg down!
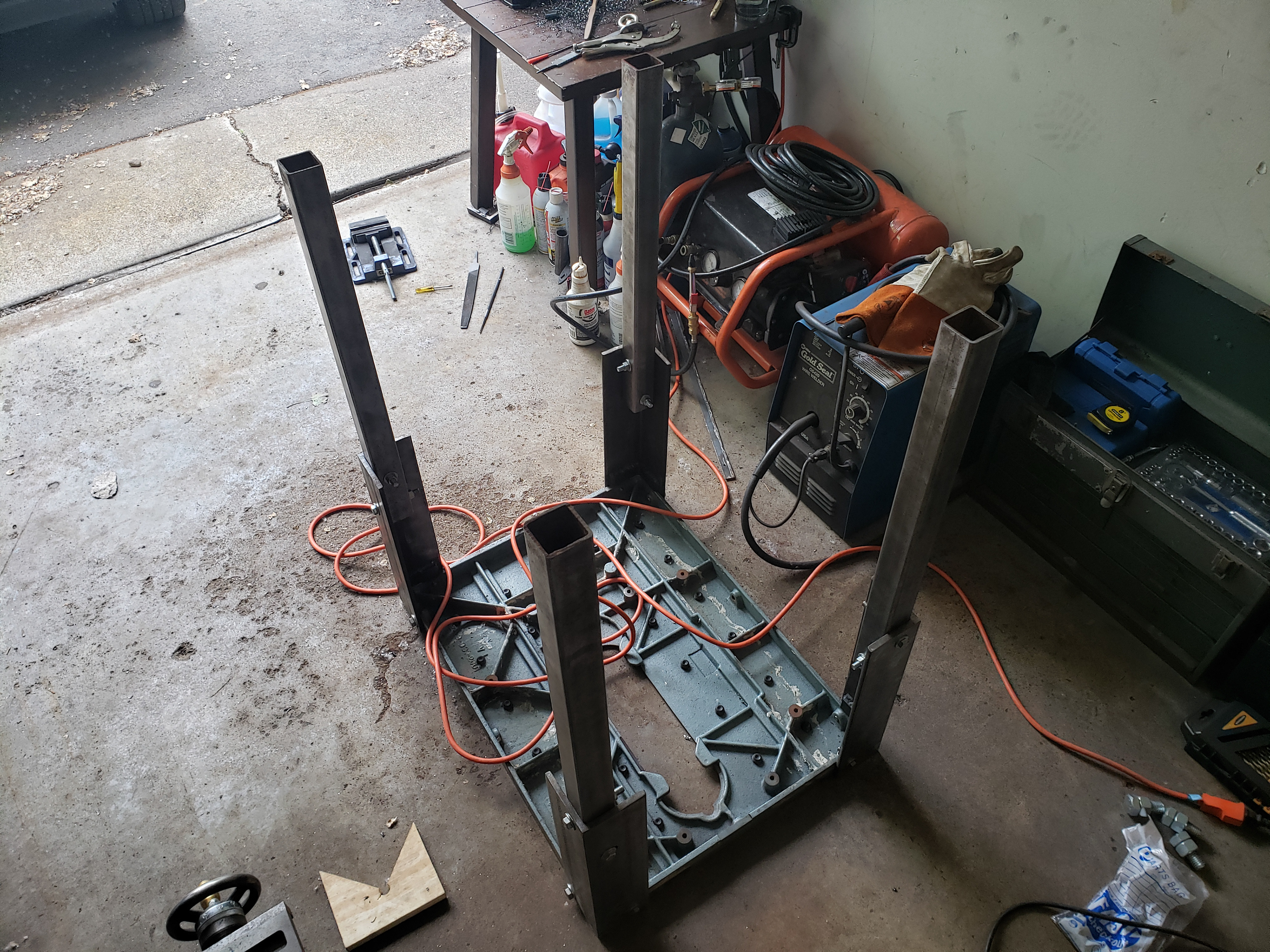
4 legs done and attached!
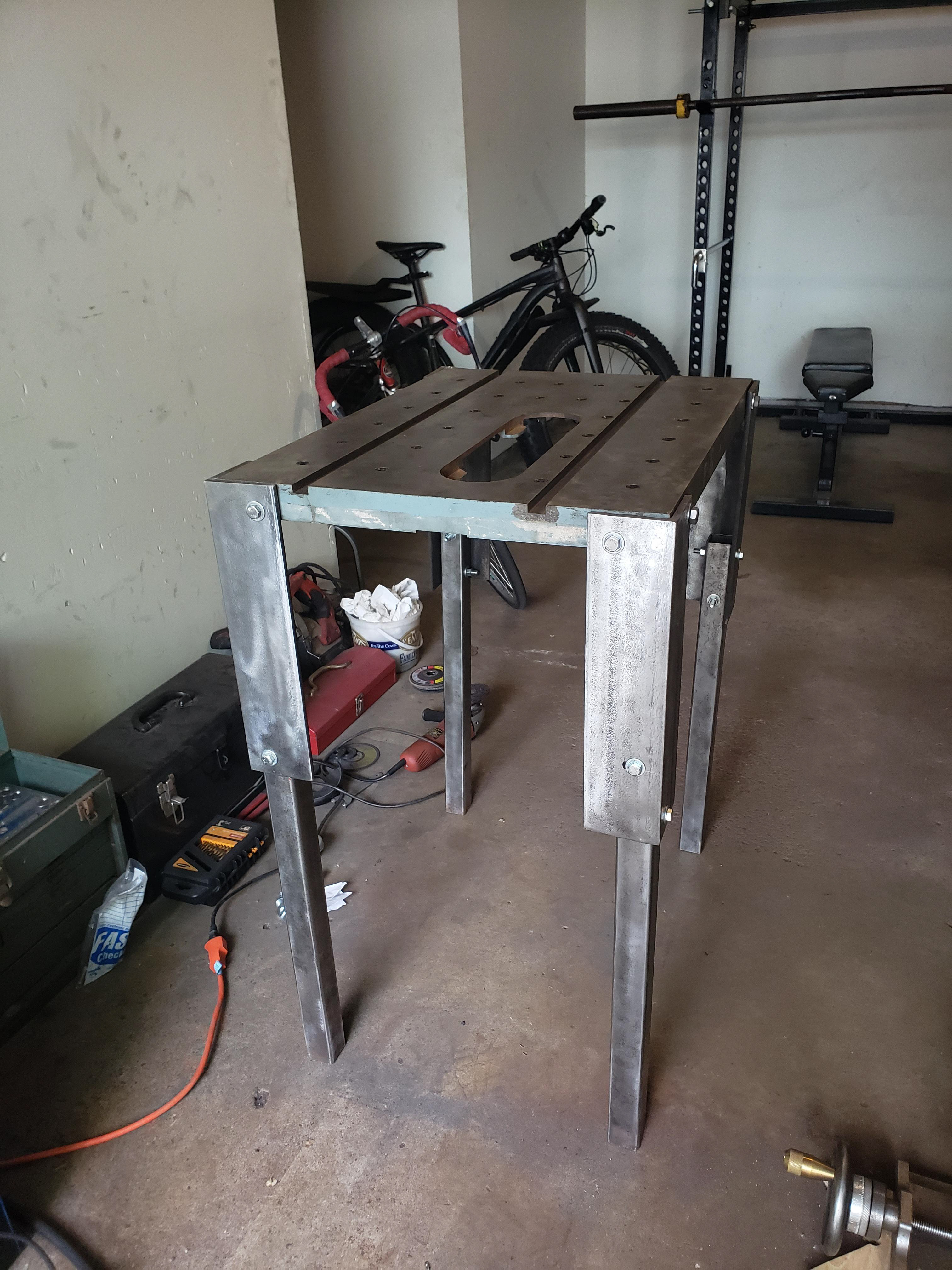
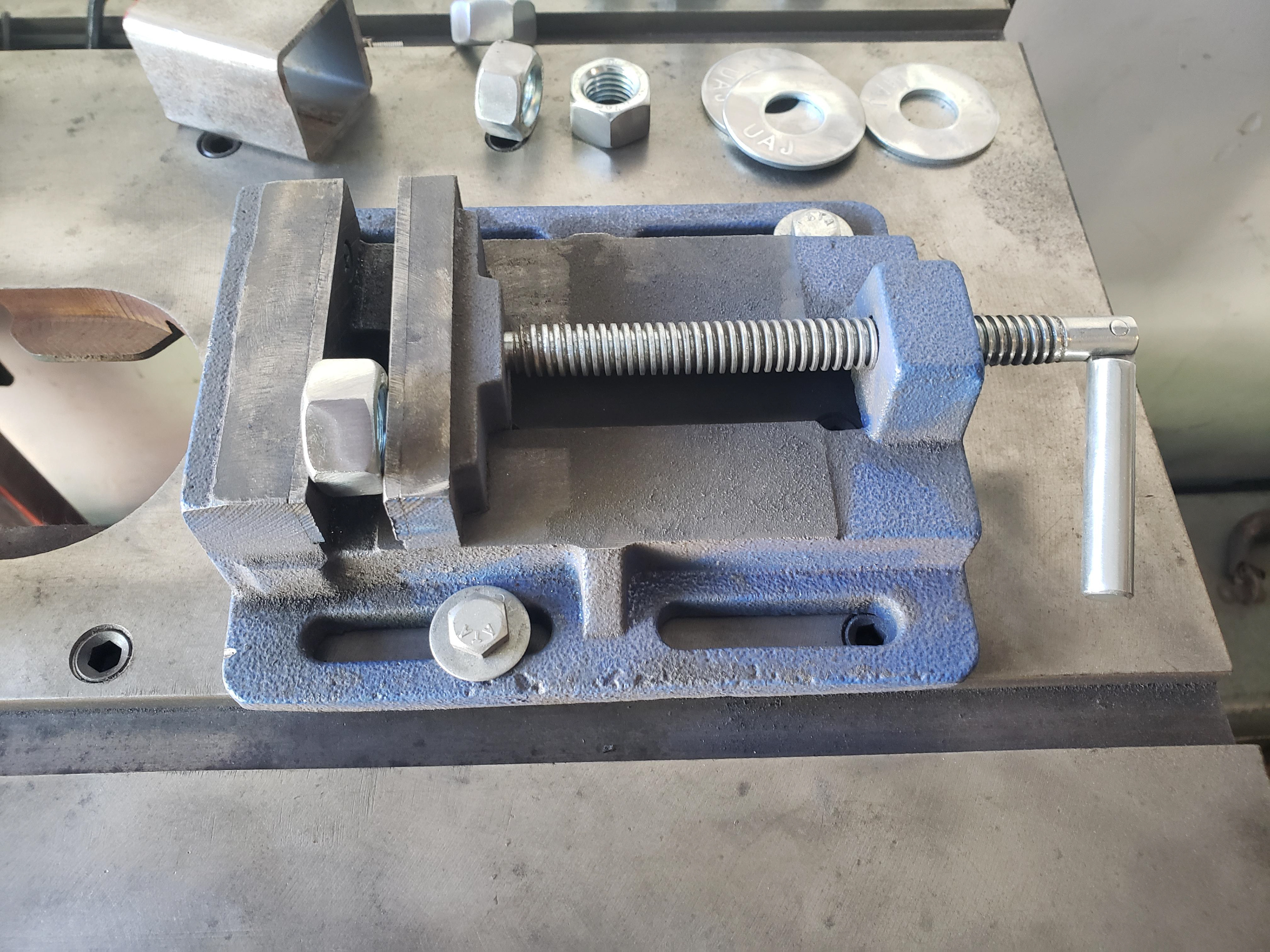
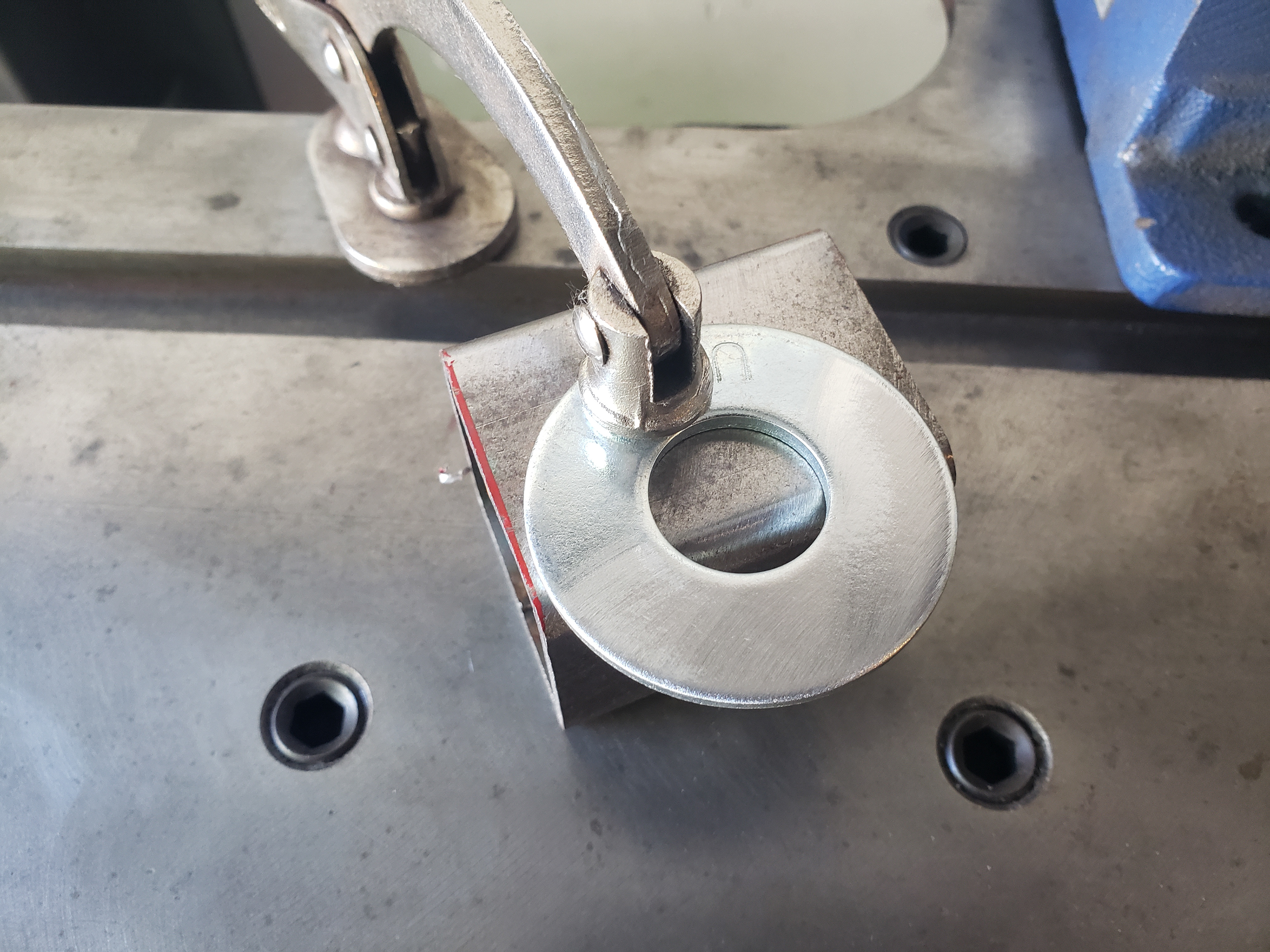
The hardware is Zinc coated so it was important to grind them prior to welding to reduce fumes (I wear a respirator anyways though).
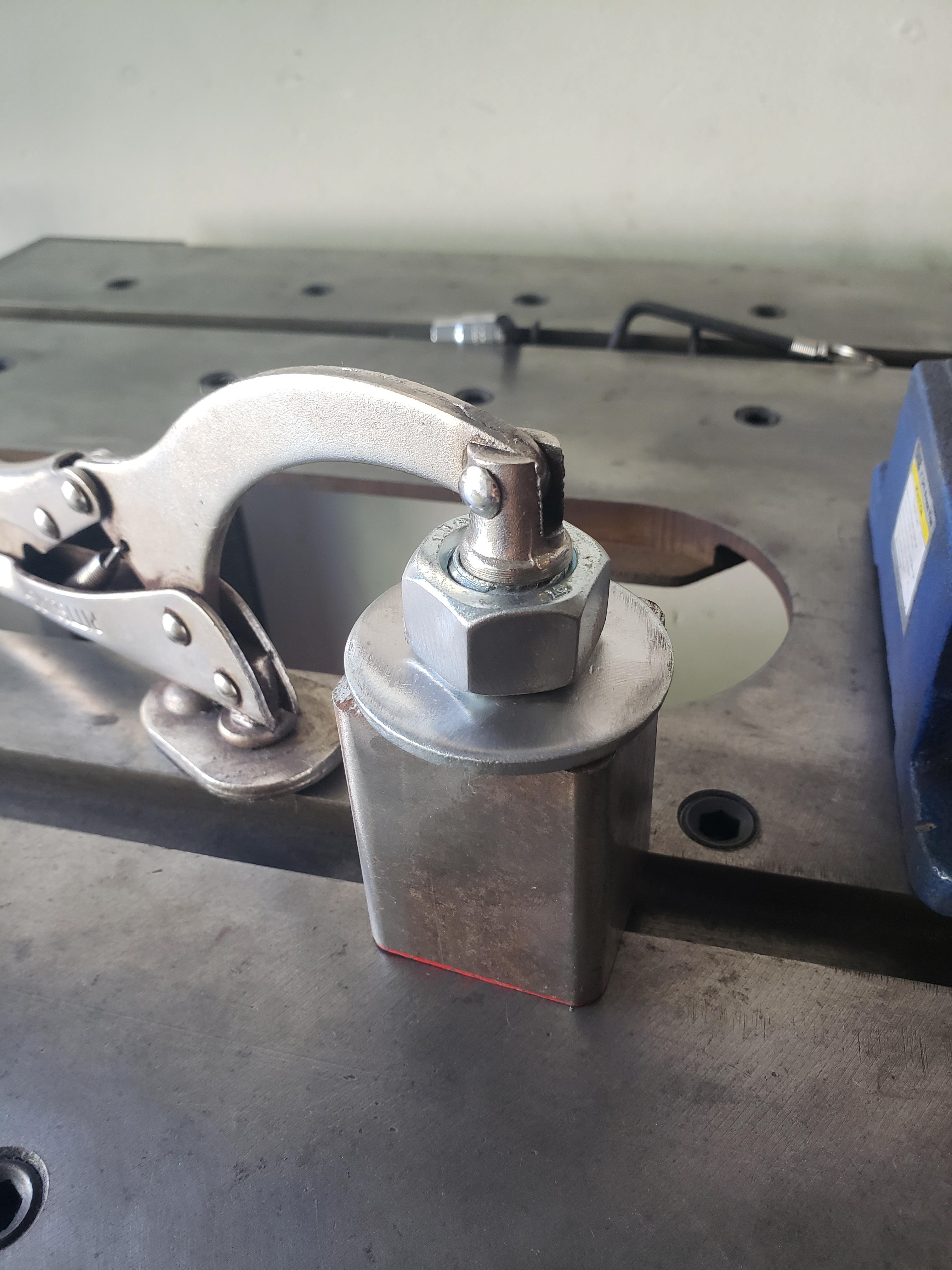
Ready for welding.
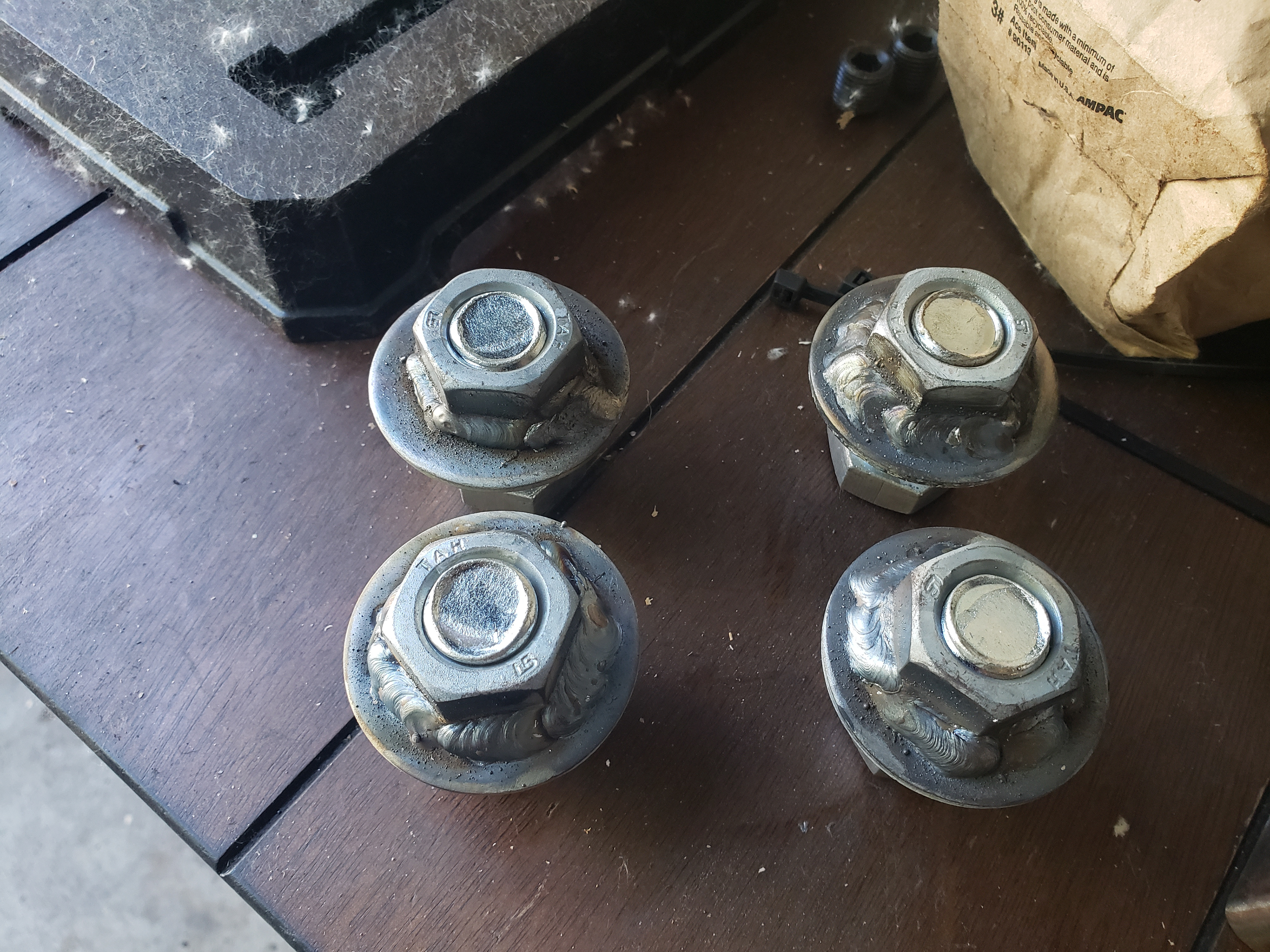
4 feet, ready to be welded to the legs.
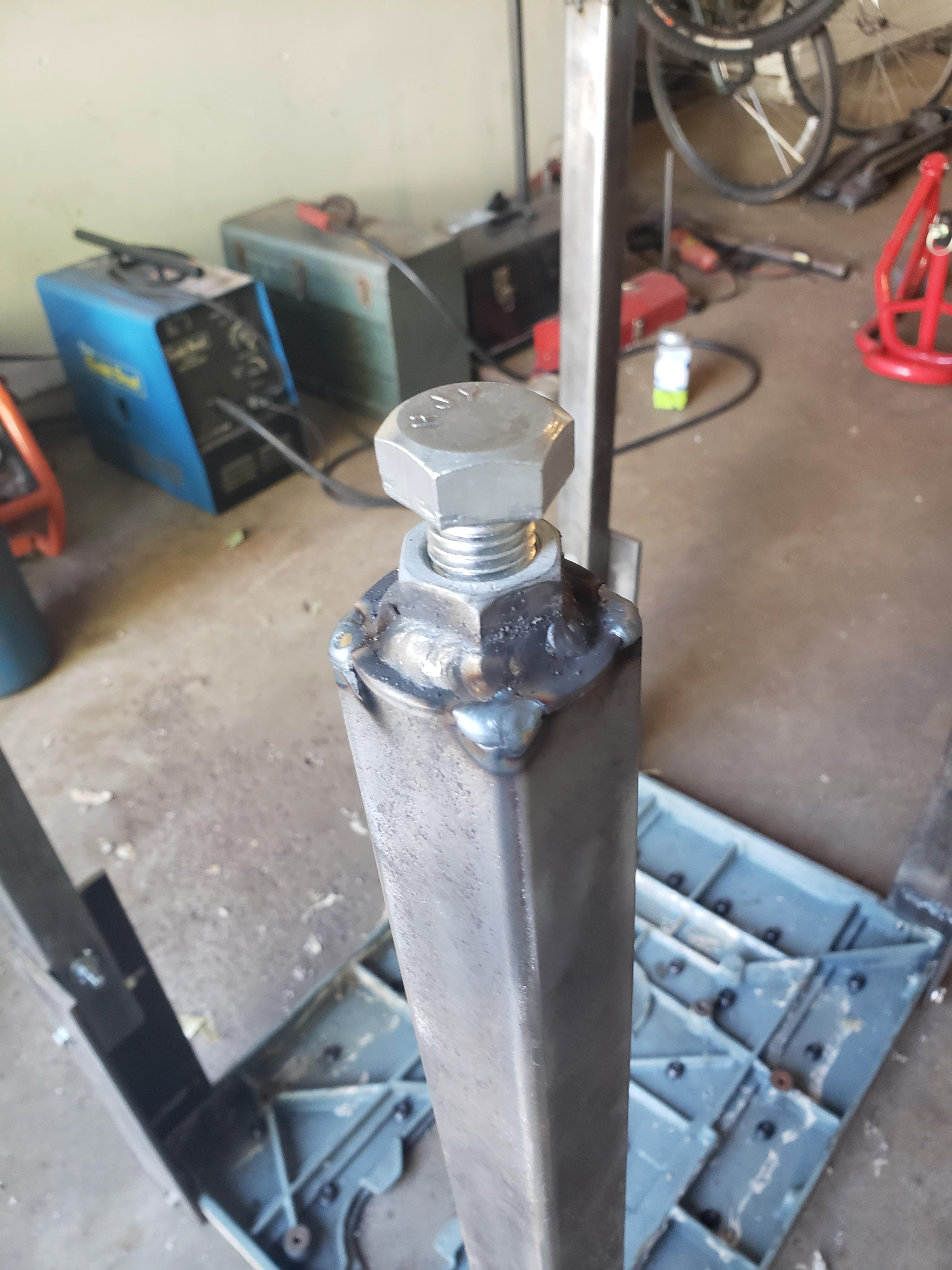
Closeup.
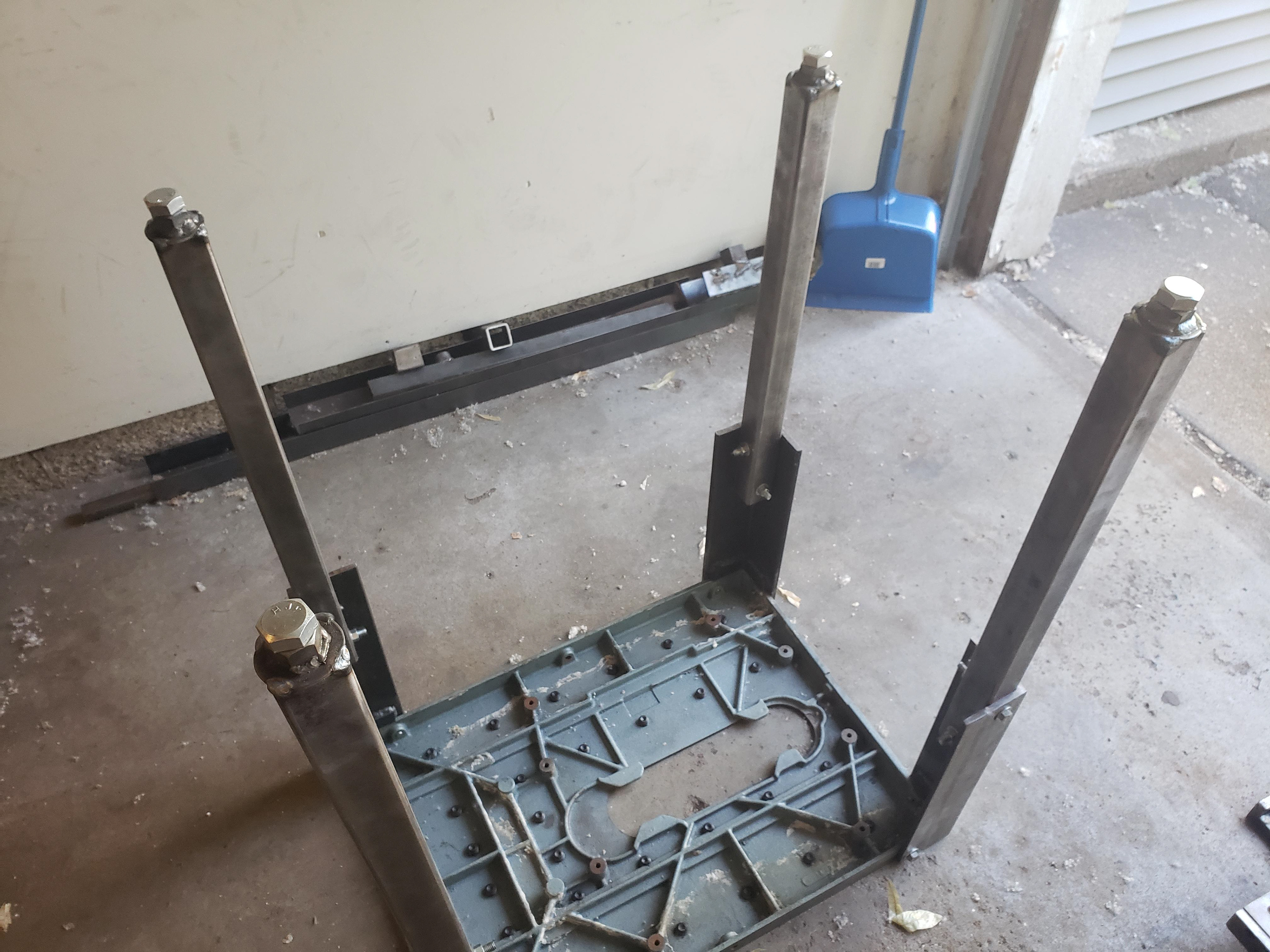
4 feet done.
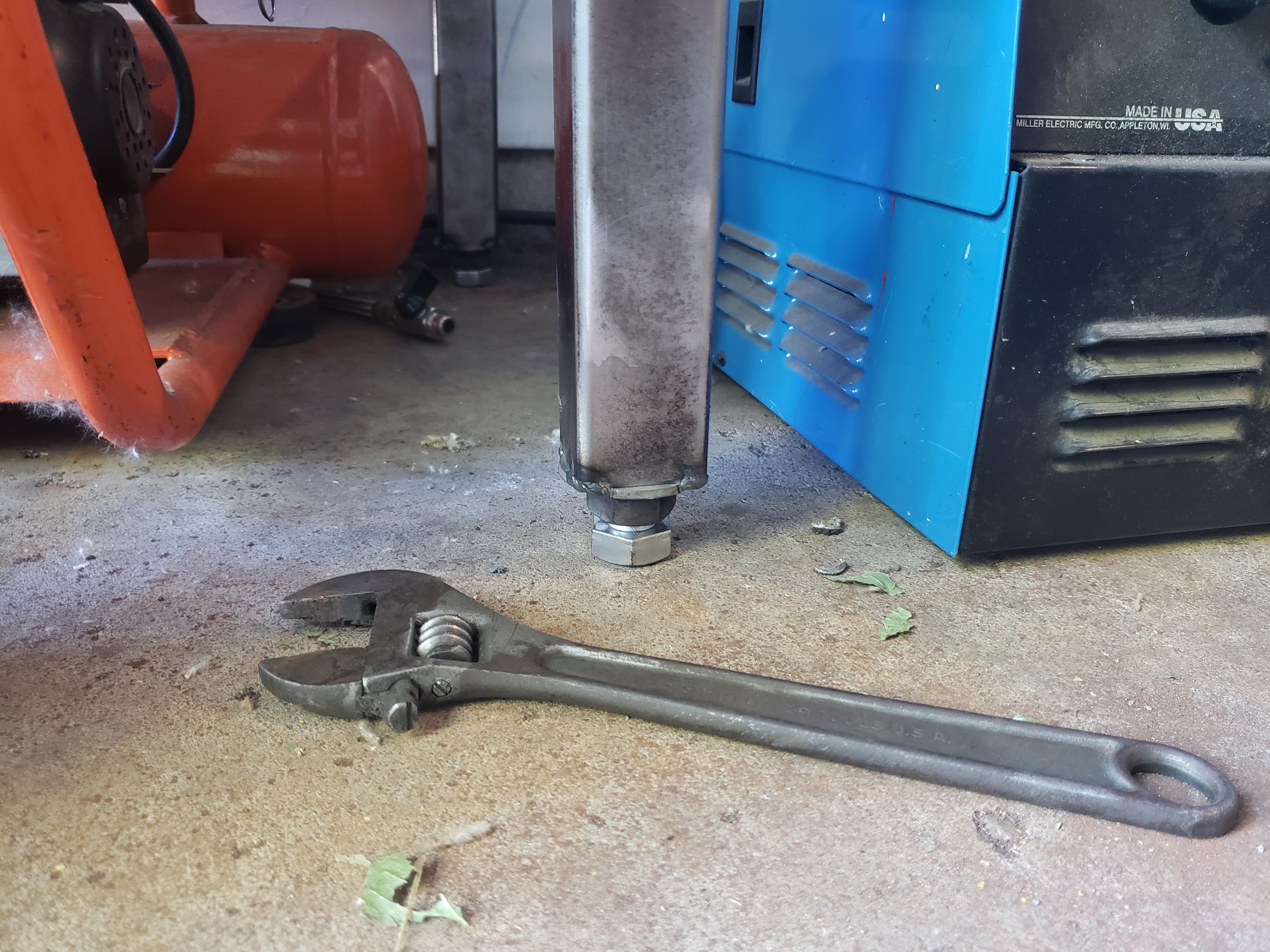
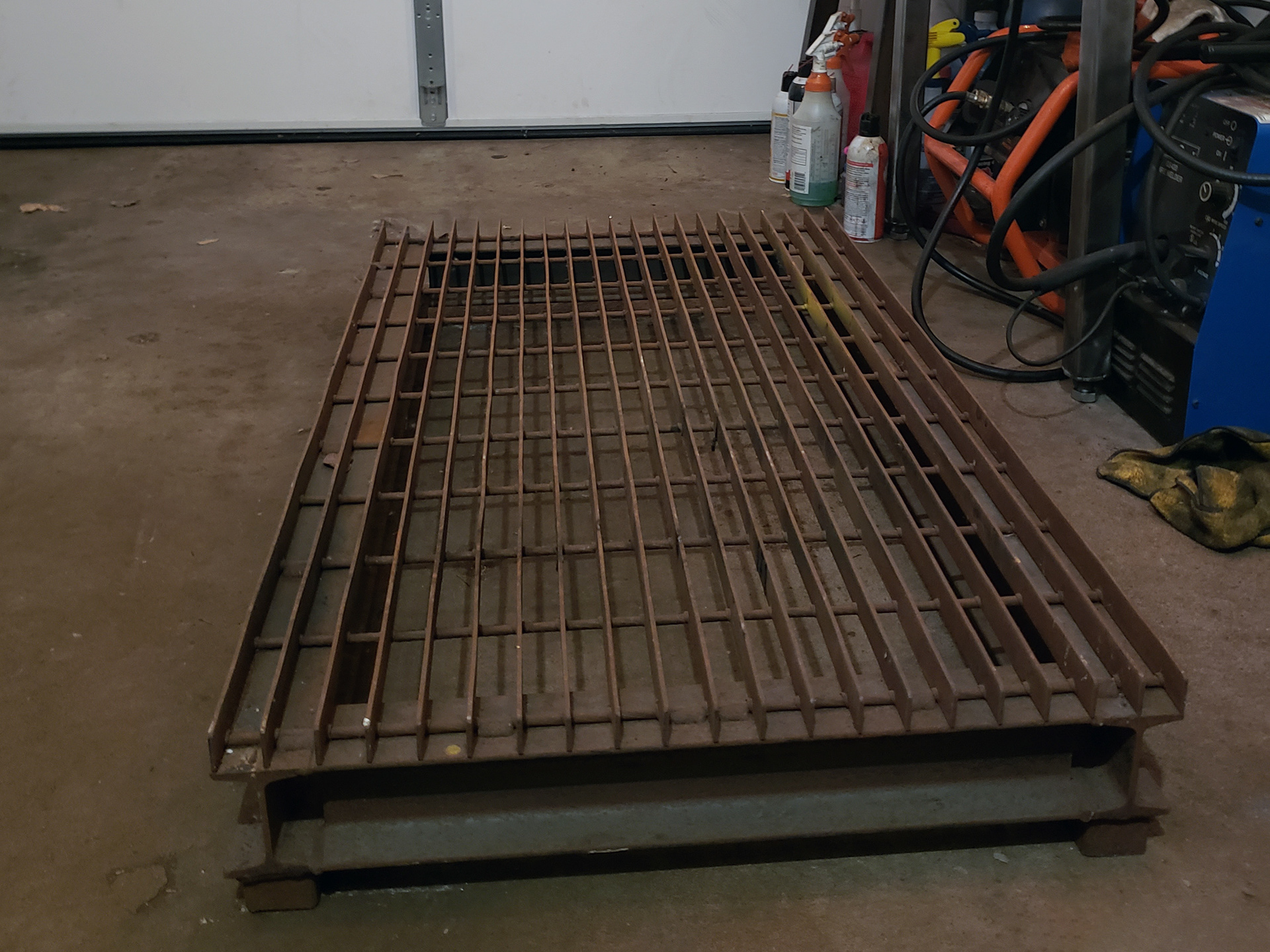
Cutting the grate free from the I-beam frame.